In the world of textile manufacturing, fabric costs play a crucial role in determining the overall profitability and competitiveness of a business. According to Techpacker, fabric expenses often account for 60 to 70% of the total cost for basic-styled garments, making precise fabric costing an essential aspect of successful operations.
Consider the following key points:
- Fabric costs can range from 50% to 70% of the total garment production costs, depending on the type of garment and the quality of the fabric used. This variance highlights the significant impact fabric selection has on overall expenses.
- Inaccurate fabric costing can lead to overpriced products, reduced market competitiveness, and decreased profit margins.
- Underestimating fabric costs can result in financial losses, as the selling price may not cover the actual production expenses.
- Accurate fabric costing enables businesses to make informed decisions regarding pricing, supplier selection, and inventory management.
Fabric Type | Percentage of Total Garment Cost |
---|---|
Basic Cotton | 50% - 60% |
Specialty Fabrics | 60% - 70% |
Luxury Materials | 65% - 75% |
To ensure the long-term success and growth of a textile business, it is imperative to prioritize accurate fabric costing. By understanding the true costs associated with each fabric type and production process, businesses can optimize their operations, maintain profitability, and remain competitive in the ever-evolving textile industry. Implementing a robust fabric cost estimator can streamline this process and provide valuable insights for informed decision-making.
Key Factors Affecting Fabric Costs
Several factors contribute to the overall cost of fabrics, and understanding these elements is essential for accurate fabric costing. These factors include:
-
Raw Material Type, Quality, and Quantity
- The type of fiber used, such as cotton, wool, silk, or synthetic materials, significantly impacts the cost of the fabric.
- Higher quality fibers, such as long-staple cotton or fine merino wool, command higher prices due to their superior properties and limited availability.
- The quantity of raw materials required for a specific fabric also affects the total cost, with larger quantities often resulting in lower per-unit prices.
-
Yarn Factors
- Yarn count, which refers to the thickness or fineness of the yarn, influences fabric cost. Higher yarn counts (finer yarns) generally result in higher costs.
- The spinning method used, such as ring spinning or open-end spinning, affects the quality and price of the yarn.
- Yarn brightness, achieved through mercerization or other treatments, can add to the overall cost.
-
Weaving Techniques and Loom Types
- The complexity of the weave structure, such as plain weave, twill, or jacquard, impacts the cost of the fabric. More intricate weaves require additional time and resources, leading to higher prices.
- The type of loom used, such as shuttle looms, rapier looms, or air jet looms, affects production efficiency and fabric quality, which in turn influences the cost.
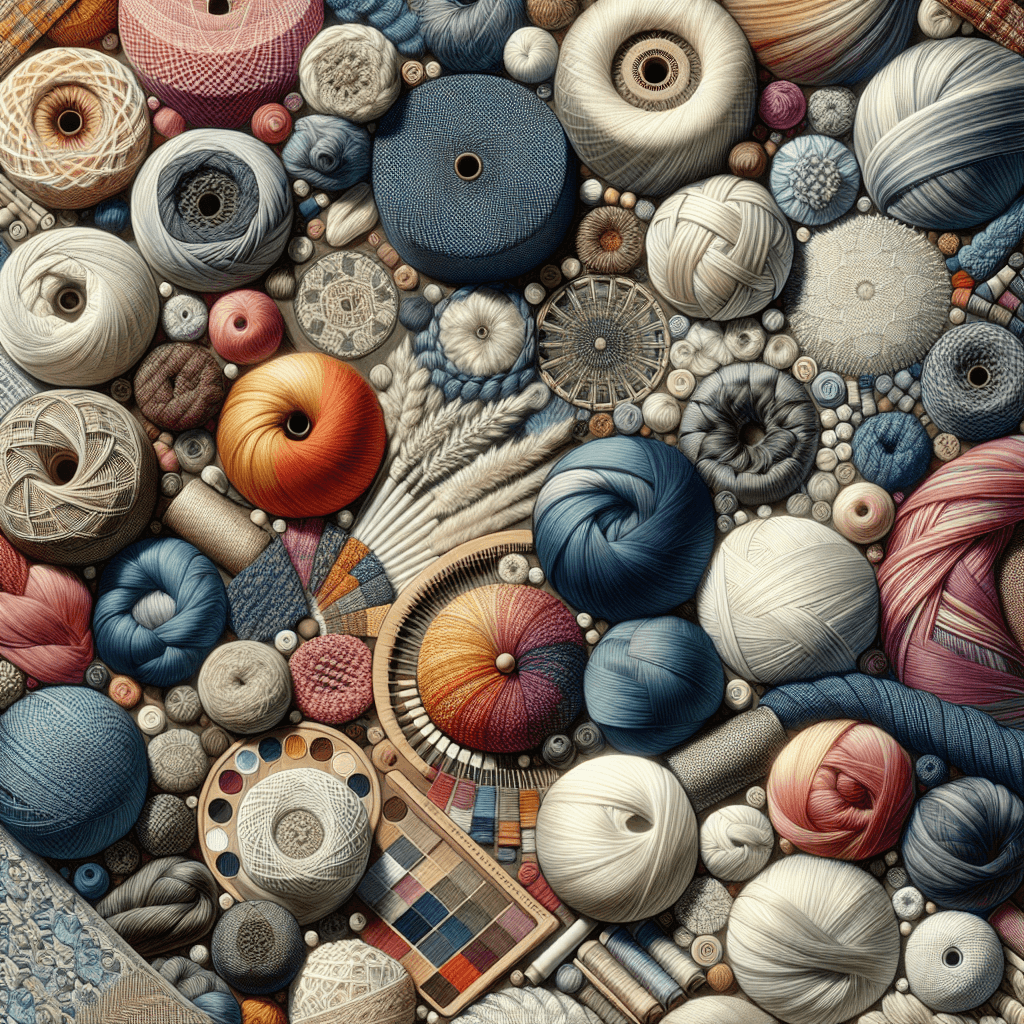
By carefully considering these key factors, textile businesses can develop a comprehensive understanding of the elements that drive fabric costs. This knowledge is crucial for accurate fabric costing and can be leveraged to optimize production processes, select appropriate raw materials, and negotiate favorable terms with suppliers. Utilizing a fabric cost estimator that takes these factors into account can greatly simplify the costing process and ensure more precise calculations.
Calculating Yarn Costs for Woven Fabrics
Yarn costs constitute a significant portion of the total fabric cost, and accurately calculating these expenses is crucial for precise fabric costing. When dealing with woven fabrics, it is essential to determine the warp and weft yarn weights using specific formulas. These formulas take into account various fabric parameters, such as:
- Ends per inch (EPI): The number of warp yarns per inch of fabric width.
- Picks per inch (PPI): The number of weft yarns per inch of fabric length.
- Yarn count: The thickness or fineness of the yarn, typically expressed in terms of Ne (English count) or Nm (metric count).
- Crimp percentage: The amount of waviness or elongation in the yarn due to the interlacing of warp and weft yarns during weaving.
To calculate the warp yarn weight, use the following formula:
Warp weight (kg) = (EPI × Fabric length × Warp count × 10^-5) / (840 × Warp crimp %)
Similarly, the weft yarn weight can be calculated using:
Weft weight (kg) = (PPI × Fabric width × Weft count × 10^-5) / (840 × Weft crimp %)
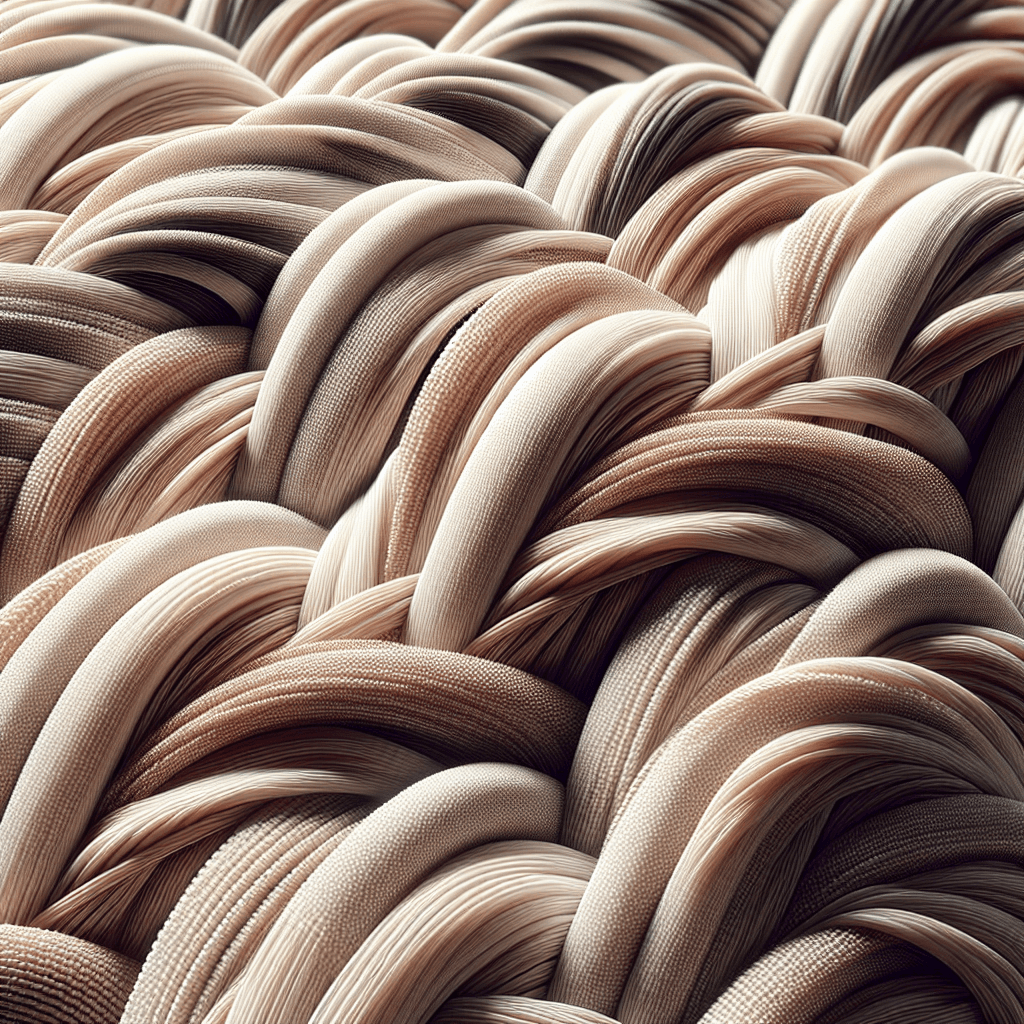
Here's an example of how these formulas can be applied:
Parameter | Value |
---|---|
Fabric length | 1000 meters |
Fabric width | 1.5 meters |
EPI | 80 |
PPI | 60 |
Warp count | 40 Ne |
Weft count | 30 Ne |
Warp crimp % | 8% |
Weft crimp % | 10% |
Using the given values, the warp and weft yarn weights can be calculated as follows:
Warp weight = (80 × 1000 × 40 × 10^-5) / (840 × 0.08) = 47.62 kg
Weft weight = (60 × 1.5 × 30 × 10^-5) / (840 × 0.10) = 3.21 kg
By accurately determining the yarn weights, textile businesses can precisely estimate the yarn costs associated with producing a specific woven fabric. This information can then be incorporated into a comprehensive fabric cost estimator to provide a detailed breakdown of the total fabric cost.
Sizing and Chemical Costs in Fabric Production
In addition to yarn costs, sizing and chemical expenses play a significant role in the overall cost of fabric production. Sizing is the process of applying a protective coating to the warp yarns to strengthen them and improve their weaving efficiency. The cost of sizing is influenced by several factors, including:
-
Chemical Cost: The price of the sizing agents used, such as starch, polyvinyl alcohol (PVA), or carboxymethyl cellulose (CMC), contributes to the overall sizing cost.
-
Power Cost: The energy consumed during the sizing process, including the operation of sizing machines and drying equipment, adds to the total expense.
-
Labor Cost: The wages paid to workers involved in the sizing process, including machine operators and material handlers, impact the sizing cost.
To calculate the sizing cost per kg of warp yarn, use the following formula:
Sizing cost per kg of warp ($/kg) = (Chemical cost + Power cost + Labor cost) / Warp yarn sized (kg)
Furthermore, the sizing cost per meter of fabric can be determined using:
Sizing cost per meter of fabric ($/m) = Sizing cost per kg of warp × Warp weight per meter of fabric
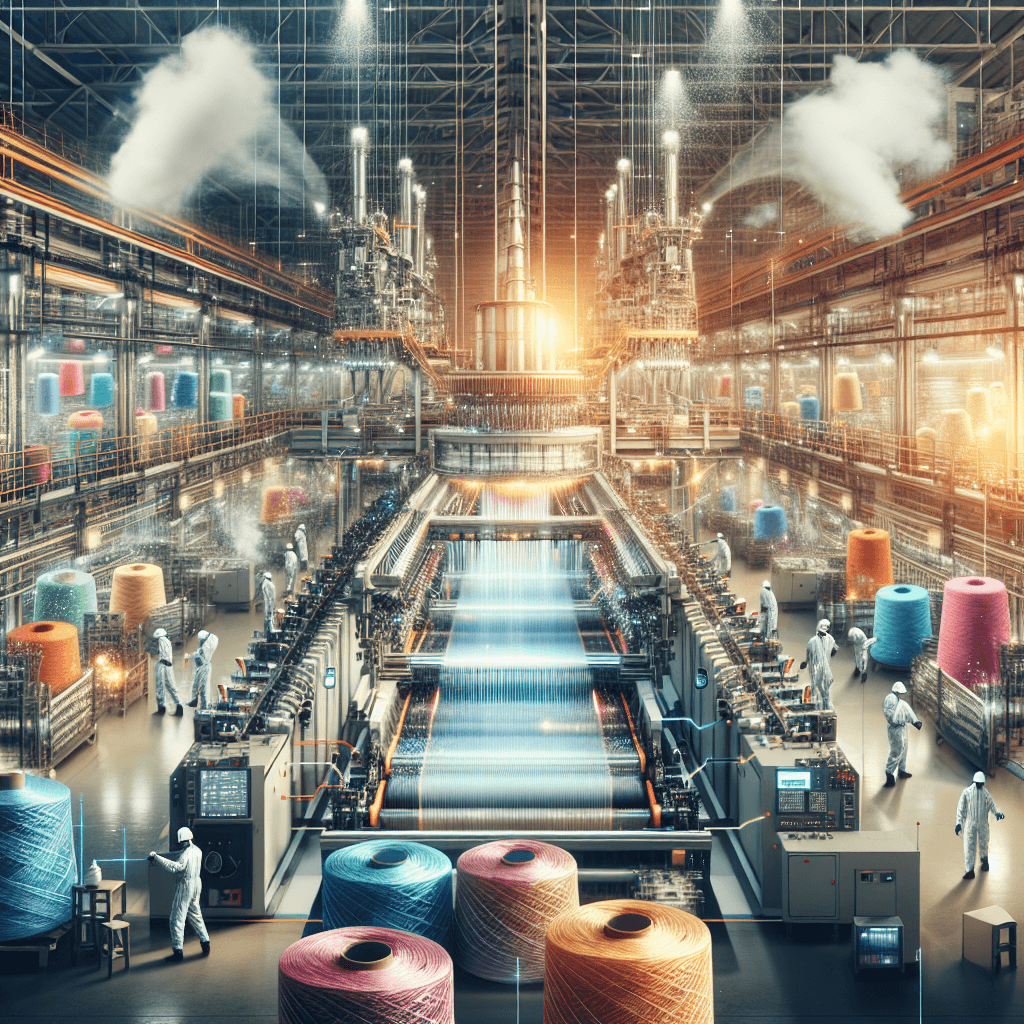
Consider an example where the sizing cost breakdown is as follows:
Cost Component | Value |
---|---|
Chemical cost | $500 |
Power cost | $200 |
Labor cost | $300 |
Warp yarn sized | 1000 kg |
Using the provided values, the sizing cost per kg of warp and per meter of fabric can be calculated:
Sizing cost per kg of warp = ($500 + $200 + $300) / 1000 kg = $1/kg
Sizing cost per meter of fabric = $1/kg × Warp weight per meter of fabric
By accurately calculating the sizing and chemical costs, textile businesses can gain a more comprehensive understanding of the expenses associated with fabric production. This information can be incorporated into a fabric cost estimator to provide a detailed breakdown of the total fabric cost, enabling informed decision-making and cost optimization strategies.
Weaving Costs: A Comprehensive Breakdown
Weaving is a crucial stage in fabric production, and understanding the costs associated with this process is essential for accurate fabric costing. Several factors contribute to the total weaving cost, including:
-
Power Cost: The energy consumed by weaving machines, lighting, and other equipment in the weaving department.
-
Labor Cost: The wages paid to weavers, loom operators, and other personnel involved in the weaving process.
-
Maintenance Cost: The expenses incurred for regular maintenance, repairs, and replacement of weaving machine parts to ensure optimal performance and minimize downtime.
-
Depreciation Cost: The cost of the gradual wear and tear of weaving machines and equipment over their useful life.
To calculate the weaving cost per meter of fabric, use the following formula:
Weaving cost per meter ($/m) = (Power cost + Labor cost + Maintenance cost + Depreciation cost) / Total fabric production (m)
Additionally, the weaving cost per pick can be determined using:
Weaving cost per pick ($/pick) = Weaving cost per meter / Picks per meter

Consider an example where the weaving cost breakdown for a fabric production run is as follows:
Cost Component | Value |
---|---|
Power cost | $1000 |
Labor cost | $2500 |
Maintenance cost | $500 |
Depreciation cost | $1000 |
Total fabric production | 10,000 meters |
Picks per meter | 1000 |
Using the provided values, the weaving cost per meter of fabric and per pick can be calculated:
Weaving cost per meter = ($1000 + $2500 + $500 + $1000) / 10,000 m = $0.50/m
Weaving cost per pick = $0.50/m / 1000 picks/m = $0.0005/pick
By breaking down the weaving costs and calculating the expenses per meter of fabric and per pick, textile businesses can gain valuable insights into the efficiency and profitability of their weaving operations. This information can be integrated into a fabric cost estimator to provide a comprehensive analysis of the total fabric cost, enabling data-driven decision-making and cost optimization strategies.
Dyeing and Finishing Expenses in Fabric Manufacturing
Dyeing and finishing processes play a vital role in enhancing the appearance, performance, and value of fabrics. These processes also contribute to the overall cost of fabric production. Several variables influence the dyeing costs, including:
-
Lot Size: The quantity of fabric being dyed in a single batch. Larger lot sizes often result in lower per-unit dyeing costs due to economies of scale.
-
Fabric Width: The width of the fabric being dyed. Wider fabrics require more dye and processing time, leading to higher dyeing costs.
-
Dye Type and Quality: The type of dye used, such as reactive, disperse, or vat dyes, and its quality can significantly impact the cost. Higher-quality dyes often come with a higher price tag but offer better colorfastness and reproducibility.
-
Dyeing Process: The specific dyeing method employed, such as exhaustion dyeing, continuous dyeing, or pad dyeing, can affect the cost due to differences in equipment, energy consumption, and labor requirements.
In addition to dyeing, fabrics undergo various finishing treatments to improve their properties and appearance. Some common finishing processes include:
- Sanforizing: A shrinkage control process that minimizes residual shrinkage in the fabric.
- Mercerizing: A treatment that improves the luster, strength, and dye affinity of cotton fabrics.
- Softening: The application of softening agents to enhance the fabric's hand feel and drape.
- Anti-microbial Treatment: The incorporation of antimicrobial agents to prevent the growth of bacteria and fungi on the fabric.
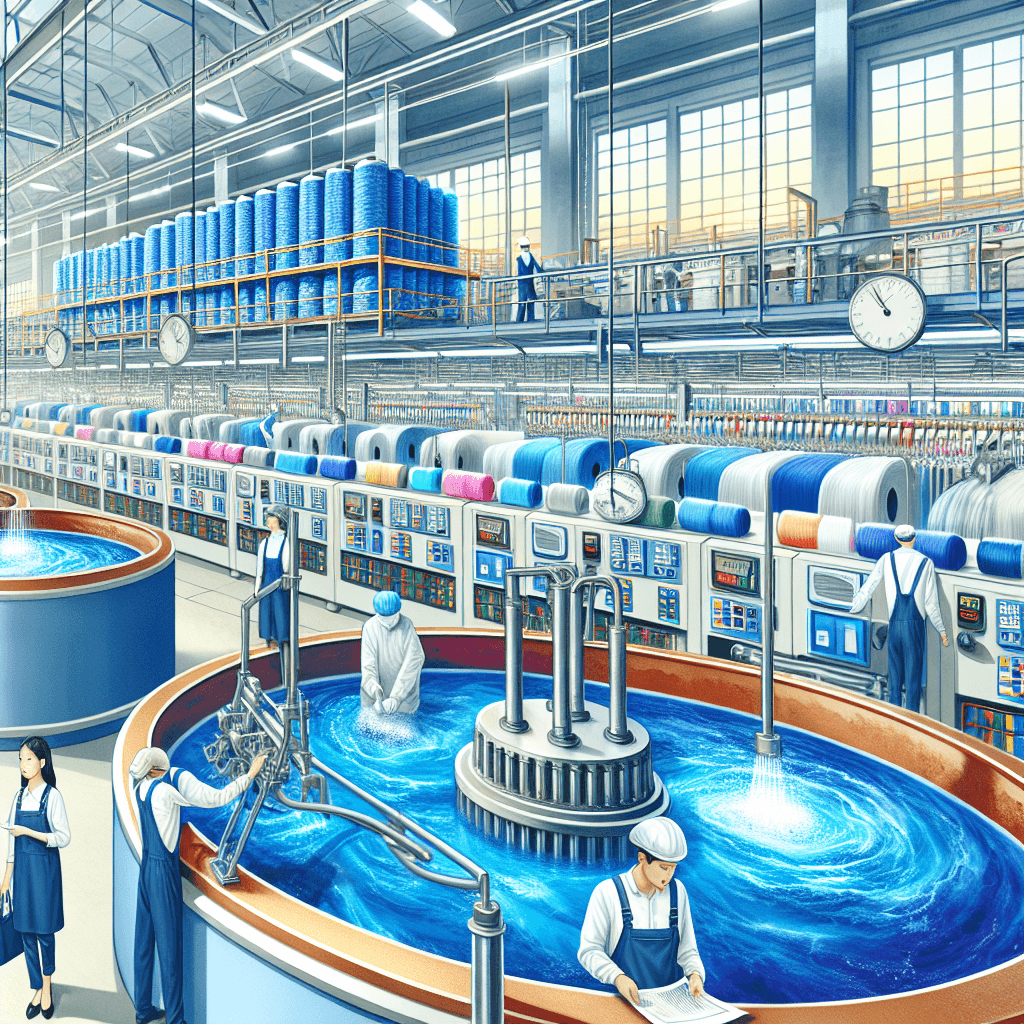
The cost of each finishing process varies depending on the type of treatment, the chemicals and equipment used, and the processing time required. To accurately estimate the dyeing and finishing expenses, consider the following factors:
Factor | Impact on Cost |
---|---|
Dye Cost | Higher-quality dyes and specialty dyes tend to be more expensive. |
Chemical Cost | The cost of auxiliary chemicals, such as leveling agents, pH regulators, and softeners, adds to the overall expense. |
Energy Cost | The energy consumed during dyeing and finishing processes, including heating, cooling, and drying, contributes to the cost. |
Labor Cost | The wages paid to operators and technicians involved in dyeing and finishing operations impact the total cost. |
Wastewater Treatment | The cost of treating and disposing of wastewater generated during dyeing and finishing processes should be considered. |
By carefully analyzing the dyeing and finishing expenses, textile businesses can gain a better understanding of the factors that influence the total fabric cost. This information can be incorporated into a fabric cost estimator to provide a comprehensive breakdown of the production costs, enabling informed decision-making and cost optimization strategies.
Accounting for Wastage and Shrinkage in Fabric Costing
Wastage and shrinkage are inevitable aspects of fabric production that can significantly impact the overall cost. Accurately accounting for these factors is crucial for precise fabric costing and maintaining profitability.
Wastage refers to the loss of fabric during various stages of production, such as:
- Cutting: Fabric waste generated during the cutting process due to pattern layout inefficiencies or cutting errors.
- Sewing: Fabric loss that occurs during the sewing process, including seam allowances, thread wastage, and end-of-roll wastage.
- Defects: Fabric that is discarded due to defects, such as weaving faults, stains, or inconsistent dyeing.
Shrinkage, on the other hand, is the reduction in fabric dimensions that occurs during washing, dyeing, or finishing processes. The amount of shrinkage varies depending on the fabric type, fiber content, and processing methods used.
Typical wastage and shrinkage percentages in fabric production are as follows:
Fabric Type | Wastage % | Shrinkage % |
---|---|---|
Woven Cotton | 3-5% | 5-10% |
Knitted Cotton | 2-4% | 3-8% |
Polyester | 2-4% | 1-3% |
Nylon | 2-4% | 1-3% |
To account for wastage and shrinkage in fabric costing, follow these steps:
- Determine the expected wastage and shrinkage percentages based on the fabric type and production processes.
- Calculate the total fabric required, including wastage and shrinkage allowances, using the following formula:
Total fabric required (m) = Fabric consumption (m) × (1 + Wastage %) × (1 + Shrinkage %)
- Use the total fabric required to calculate the fabric cost, considering the price per meter of the fabric.
For example, if a garment requires 2 meters of woven cotton fabric with a wastage of 4% and a shrinkage of 8%, and the fabric price is $5 per meter, the total fabric cost can be calculated as follows:
Total fabric required = 2 m × (1 + 0.04) × (1 + 0.08) = 2.25 m
Fabric cost = 2.25 m × $5/m = $11.25
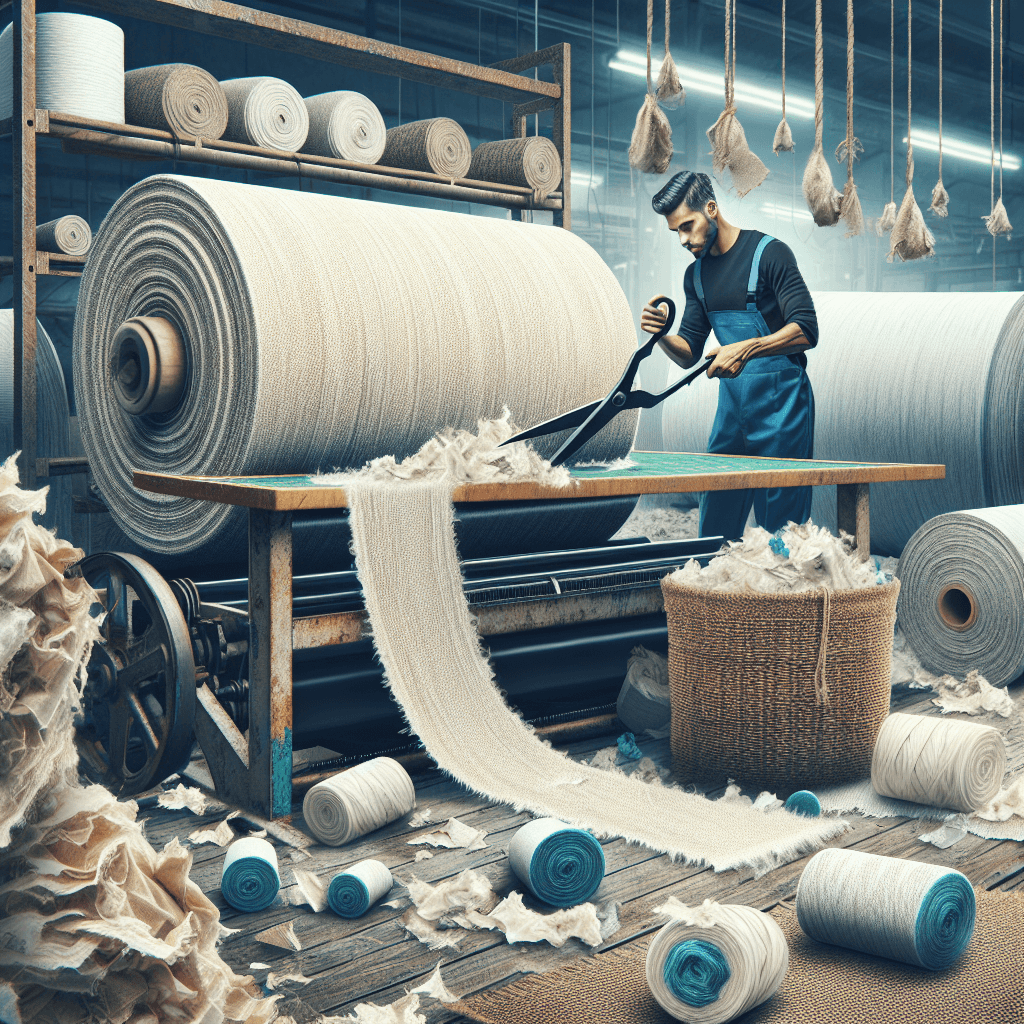
By accurately accounting for wastage and shrinkage, textile businesses can ensure that their fabric costing is comprehensive and reflective of the true production costs. This information can be integrated into a fabric cost estimator to provide a detailed breakdown of the fabric expenses, enabling better decision-making and cost control measures.
Introducing the Fabric Cost Estimator: A Game-Changer for Your Business
In the fast-paced world of textile manufacturing, having a reliable and efficient tool for calculating fabric costs is essential. That's where the Fabric Cost Estimator comes in – a powerful, user-friendly solution designed to streamline your costing process and improve your bottom line.
The Fabric Cost Estimator is a comprehensive tool that takes into account all the critical factors involved in fabric production, including:
- Raw material costs
- Yarn and weaving expenses
- Dyeing and finishing costs
- Wastage and shrinkage allowances
- Labor and overhead expenses
By inputting your specific fabric parameters and production details, the Fabric Cost Estimator quickly generates accurate cost estimates, saving you time and effort in manual calculations.
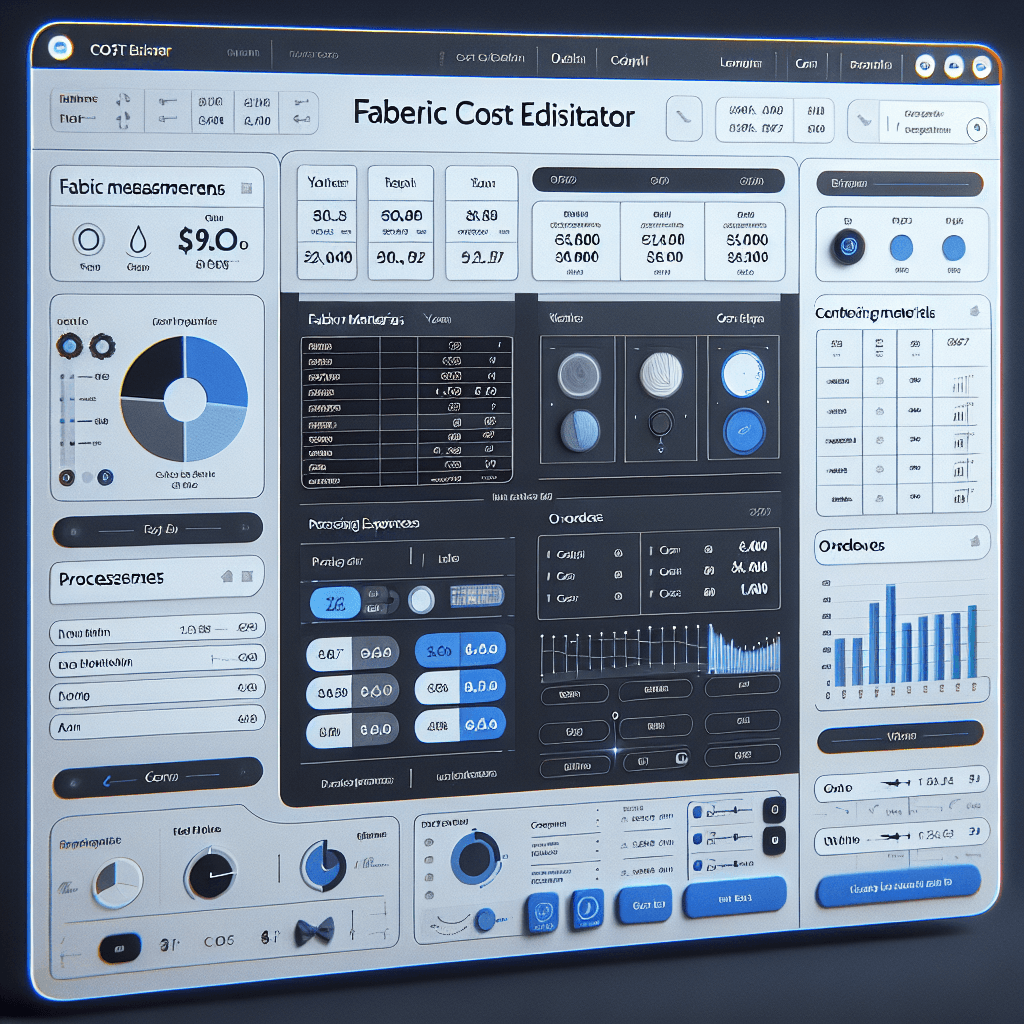
Key features of the Fabric Cost Estimator include:
-
User-Friendly Interface: The intuitive, easy-to-navigate interface makes it simple for users of all skill levels to input data and obtain results quickly.
-
Customizable Inputs: The tool allows you to customize various inputs, such as fabric dimensions, yarn counts, and processing costs, to match your unique production requirements.
-
Detailed Cost Breakdown: The Fabric Cost Estimator provides a detailed breakdown of all cost components, enabling you to identify areas for potential savings and optimization.
-
Scenario Analysis: With the ability to create and compare multiple scenarios, you can easily assess the impact of different fabric options, production methods, or cost-saving strategies on your overall expenses.
-
Integration Capabilities: The Fabric Cost Estimator can be seamlessly integrated with your existing ERP or inventory management systems, ensuring data consistency and accuracy across your organization.
By leveraging the power of the Fabric Cost Estimator, your textile business can:
- Reduce the time and effort spent on manual cost calculations
- Improve the accuracy and reliability of your fabric costing
- Identify opportunities for cost optimization and efficiency improvements
- Make data-driven decisions based on comprehensive cost insights
- Enhance collaboration and communication among team members
Investing in a Fabric Cost Estimator is a smart move for any textile business looking to stay competitive, optimize costs, and improve overall profitability. By streamlining your costing process and gaining valuable insights into your fabric expenses, you'll be well-equipped to tackle the challenges of today's dynamic textile industry.
How the Fabric Cost Estimator Works: A Step-by-Step Guide
Using the Fabric Cost Estimator is a straightforward process that can be mastered quickly, even by those without extensive technical expertise. Follow this step-by-step guide to understand how the tool works and how you can leverage its capabilities to optimize your fabric costing process.
-
Input Fabric Dimensions:
- Enter the length and width of the fabric you wish to produce.
- Specify the unit of measurement (e.g., meters, yards) for accurate calculations.
-
Select Fabric Type and Composition:
- Choose the type of fabric you're working with, such as woven, knitted, or non-woven.
- Specify the fiber composition (e.g., 100% cotton, 80% polyester/20% spandex) to account for material costs.
-
Input Yarn Details:
- Enter the yarn count and type for both warp and weft yarns (if applicable).
- Specify the yarn price per unit weight to calculate yarn costs accurately.
-
Enter Weaving or Knitting Specifications:
- Input the number of ends per inch (EPI) and picks per inch (PPI) for woven fabrics.
- For knitted fabrics, specify the machine gauge and stitch density.
-
Add Dyeing and Finishing Details:
- Select the dyeing method (e.g., yarn dyeing, piece dyeing) and type of dye used.
- Specify the finishing processes required, such as sanforizing, mercerizing, or anti-microbial treatment.
- Input the associated costs for each dyeing and finishing process.
-
Account for Wastage and Shrinkage:
- Enter the expected wastage percentage based on your production process and historical data.
- Specify the anticipated shrinkage percentage for the chosen fabric type and composition.
-
Include Labor and Overhead Costs:
- Input the hourly labor rates for various production stages, such as weaving, dyeing, and finishing.
- Specify the overhead costs, including utilities, rent, and equipment depreciation.
-
Generate Cost Estimate:
- Click the "Calculate" button to generate a detailed cost estimate based on your inputs.
- Review the breakdown of costs, including raw materials, processing, labor, and overhead expenses.
-
Analyze and Optimize:
- Examine the cost breakdown to identify areas where costs can be optimized.
- Modify input values to explore different scenarios and assess their impact on overall costs.
- Use the insights gained to make informed decisions about fabric selection, production methods, and pricing strategies.
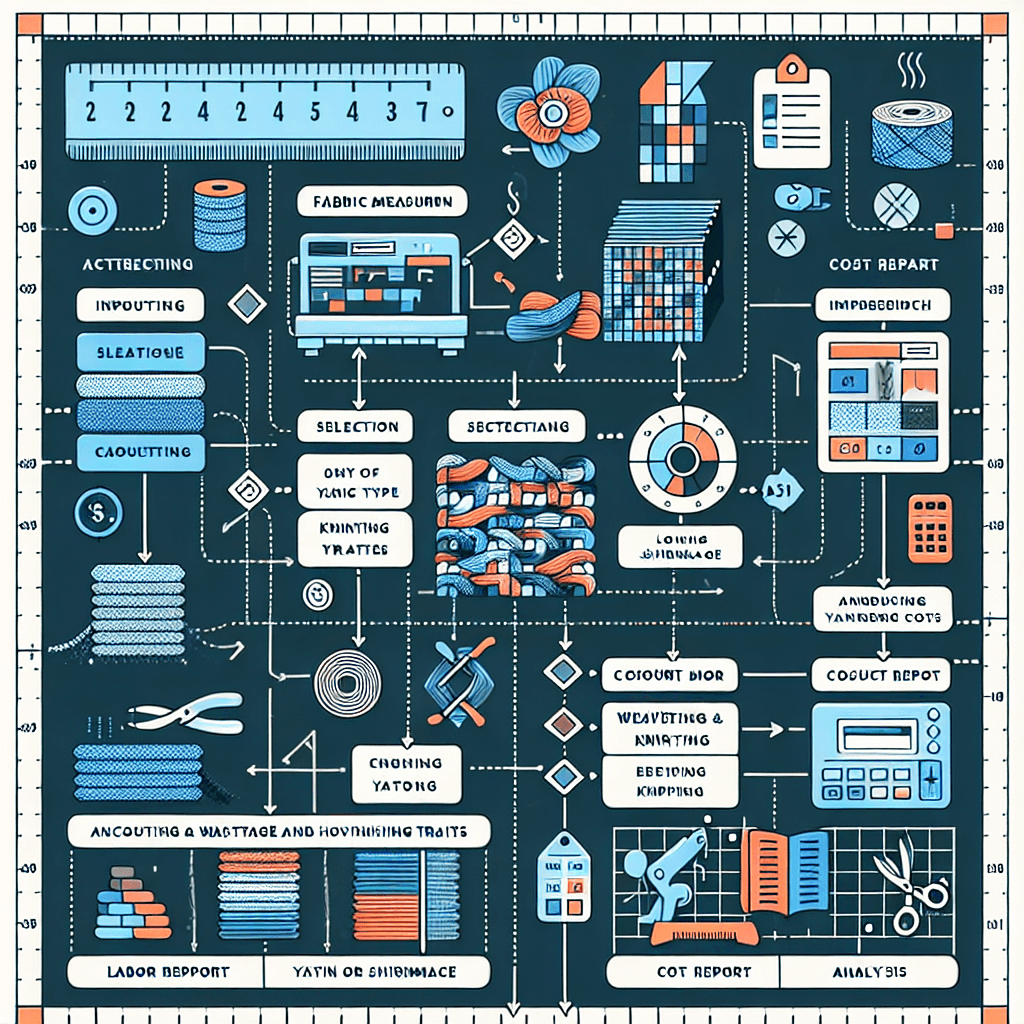
By following these steps and utilizing the Fabric Cost Estimator effectively, you can streamline your costing process, improve accuracy, and make data-driven decisions to optimize your fabric production costs. The tool's user-friendly interface and comprehensive cost breakdown enable you to gain valuable insights into your expenses and identify opportunities for cost savings and efficiency improvements.
Conclusion
In today's competitive textile industry, accurate fabric costing is essential for the success and profitability of your business. By understanding the key factors that influence fabric costs, such as raw materials, yarn and weaving expenses, dyeing and finishing processes, and wastage and shrinkage allowances, you can make informed decisions and optimize your production costs.
The Fabric Cost Estimator is a powerful tool that simplifies the costing process and provides valuable insights into your fabric expenses. With its user-friendly interface, customizable inputs, and detailed cost breakdowns, the Fabric Cost Estimator enables you to streamline your costing workflow, improve accuracy, and identify areas for cost optimization.
By leveraging the capabilities of the Fabric Cost Estimator, you can:
- Save time and effort in manual cost calculations
- Enhance the precision and reliability of your fabric costing
- Explore different scenarios and assess their impact on overall costs
- Make data-driven decisions based on comprehensive cost insights
- Improve collaboration and communication among team members
Investing in a Fabric Cost Estimator is a smart choice for any textile business looking to stay competitive, optimize costs, and boost profitability. By gaining a deeper understanding of your fabric expenses and identifying opportunities for improvement, you'll be well-equipped to navigate the challenges of the dynamic textile industry.
Take action today and revolutionize your fabric costing process with the Fabric Cost Estimator. Visit Active Calculator to learn more about how this innovative tool can transform your textile business. Discover the power of accurate, efficient, and insightful fabric costing and unlock the full potential of your production process. Don't miss this opportunity to take your textile business to the next level!