In today's fast-paced and highly competitive textile industry, businesses are constantly seeking ways to streamline their operations, improve efficiency, and boost profitability. One critical aspect of running a successful textile business is accurately estimating fabric costs. This is where a fabric cost estimator comes into play, revolutionizing the way companies manage their costing processes.
A fabric cost estimator is a powerful tool that enables textile businesses to quickly and accurately calculate the costs associated with producing a specific fabric. By inputting various parameters such as raw material prices, yarn counts, fabric weight, and processing costs, the estimator generates a detailed breakdown of the total fabric cost. This streamlined process eliminates the need for manual calculations, saving valuable time and reducing the risk of errors.
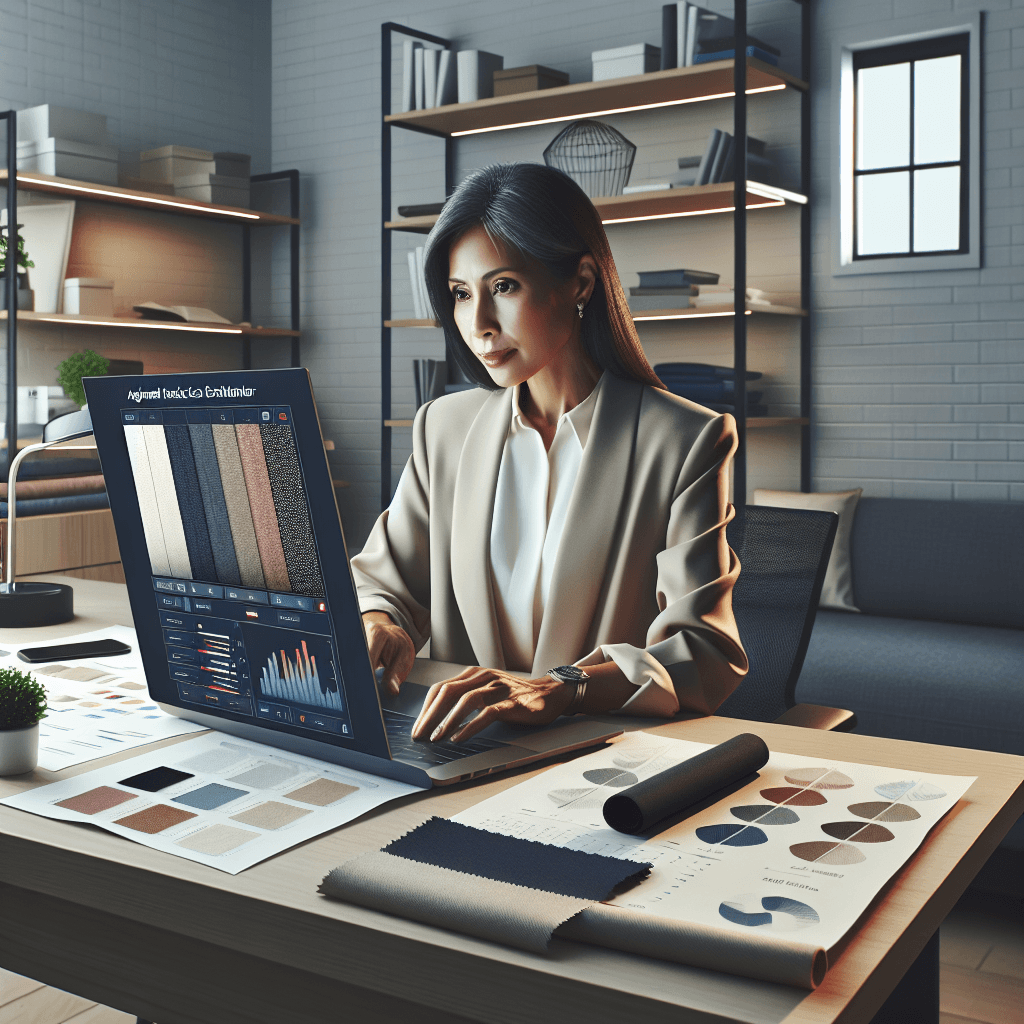
Moreover, a fabric cost estimator empowers textile businesses to make data-driven decisions when it comes to pricing and profitability. With access to accurate cost information, companies can determine the optimal selling price for their fabrics, ensuring they remain competitive in the market while maintaining healthy profit margins. This level of insight is crucial for businesses looking to stay ahead in an industry where material costs and market demands are constantly fluctuating.
The global textiles market, with a projected value added of approximately US$171.10 billion in 2024 and a compound annual growth rate (CAGR) of 5.34% over the next four years, underscores the growing need for efficient cost management tools in the sector. The total output is anticipated to reach around US$1.37 trillion in 2024, growing at a CAGR of 4.44% during the same period, further highlighting the scale and expansion of the industry (Statista).
Integrating a fabric cost estimator into your textile business's website can also significantly improve customer satisfaction. By providing transparent and competitive pricing, you build trust with your clients and demonstrate your commitment to delivering value. Customers appreciate the ability to quickly obtain accurate quotes, making the purchasing process more convenient and efficient. This enhanced user experience can lead to increased sales, customer loyalty, and positive word-of-mouth referrals.
In summary, a fabric cost estimator is an indispensable tool for any textile business looking to:
- Streamline the costing process for faster, more accurate estimates
- Enable data-driven decision making for pricing and profitability
- Improve customer satisfaction through transparent, competitive pricing
By embracing this innovative solution, textile businesses can overcome common industry challenges, optimize their operations, and position themselves for long-term success in a highly competitive market.
Key Factors That Impact Fabric Costs
When it comes to estimating the cost of a fabric, several key factors come into play. Understanding these factors is essential for textile businesses looking to accurately calculate their expenses and make informed pricing decisions. Let's take a closer look at the primary elements that influence fabric costs:
-
Raw Material Types, Quality, and Yarn Counts: The type and quality of raw materials used in fabric production have a significant impact on the overall cost. Higher-quality fibers, such as premium cotton or silk, typically come with a higher price tag compared to lower-grade alternatives. Additionally, the yarn count, which refers to the thickness or fineness of the yarn, affects the cost. Finer yarns with higher counts generally result in more expensive fabrics.
-
Fabric Weight/GSM and Construction Complexity: The weight of the fabric, measured in grams per square meter (GSM), is another crucial factor. Heavier fabrics require more raw materials, resulting in higher costs. Moreover, the complexity of the fabric construction, such as the weave or knit pattern, can influence the cost. Intricate designs and structures often involve more time and resources to produce, leading to increased expenses.
-
Additional Processes Like Sizing, Dyeing, and Finishing Treatments: Beyond the raw materials and construction, fabrics often undergo various additional processes that contribute to the final cost. Sizing, which involves applying a protective coating to the yarn, adds to the production expenses. Dyeing, whether it's solid colors or intricate patterns, also impacts the cost, with more complex designs and color combinations requiring more resources. Finally, finishing treatments, such as softening, water-repellent coatings, or antimicrobial properties, can significantly affect the overall fabric cost.
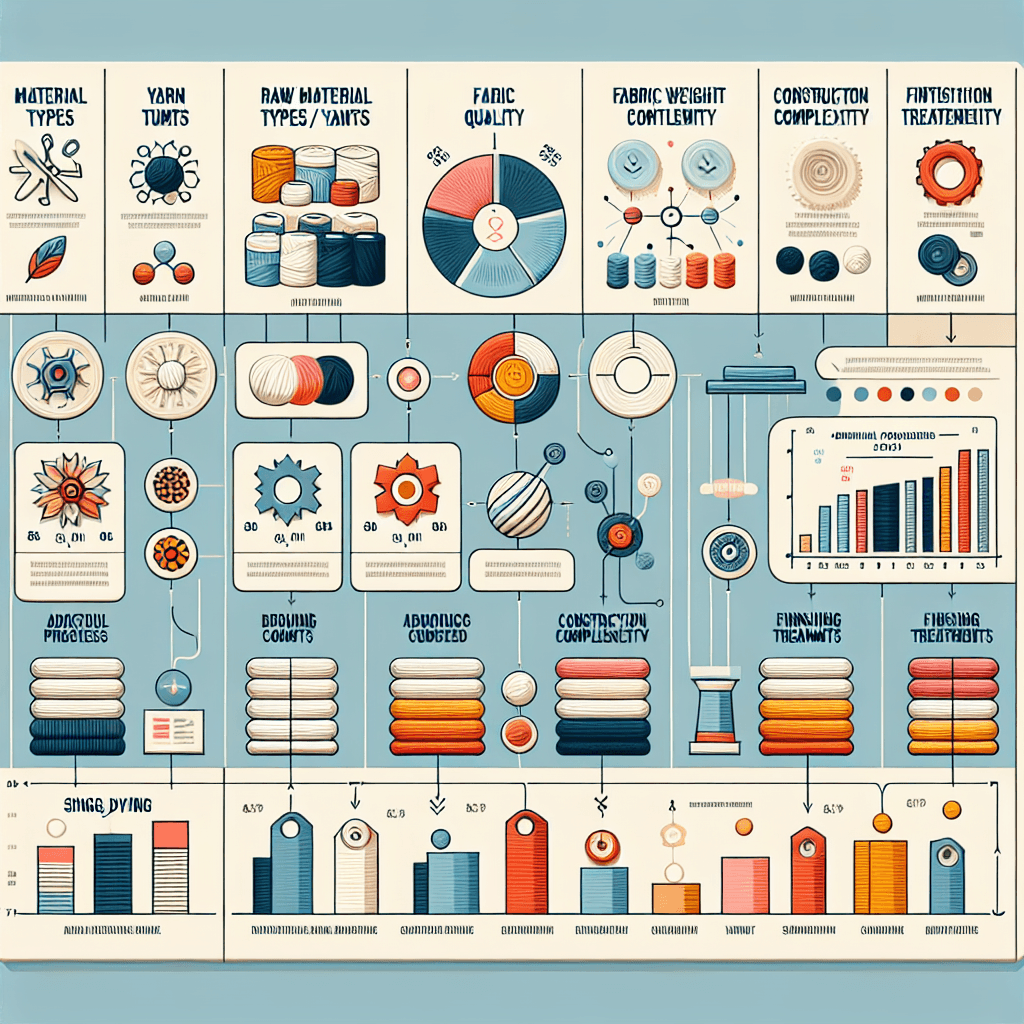
To illustrate the impact of these factors, consider the following example:
Fabric Type | Raw Material | Yarn Count | Weight (GSM) | Construction | Additional Processes | Estimated Cost |
---|---|---|---|---|---|---|
Cotton Twill | Premium Cotton | 40s/2 | 250 | 3/1 Twill | Sizing, Dyeing (Solid), Softening | $8.50/meter |
Polyester Satin | Standard Polyester | 75D | 120 | Satin Weave | Dyeing (Printed), Water-Repellent Coating | $6.75/meter |
As the table demonstrates, the combination of raw materials, yarn count, weight, construction, and additional processes can result in significant variations in fabric costs. By carefully considering these factors and utilizing a fabric cost estimator, textile businesses can accurately assess their expenses and make informed decisions to optimize their production and pricing strategies.
How to Calculate Yarn Costs for Woven Fabrics
One of the most significant components of fabric cost estimation is calculating the yarn costs for woven fabrics. Woven fabrics consist of two sets of yarns: warp yarns, which run lengthwise, and weft yarns, which run perpendicular to the warp. To accurately determine the yarn costs, textile businesses must consider several key parameters.
First, it's essential to determine the warp and weft yarn weights based on the fabric parameters. This involves considering factors such as the yarn count, ends per inch (EPI), picks per inch (PPI), crimp percentage, waste percentage, and yarn prices. The yarn count refers to the thickness or fineness of the yarn, while EPI and PPI indicate the number of warp and weft yarns per inch, respectively. Crimp percentage accounts for the waviness of the yarn in the fabric structure, and waste percentage considers the inevitable loss of yarn during the weaving process.
To calculate the total warp and weft yarn costs per meter, textile businesses can use the following formulas:
Warp Yarn Cost per Meter:
Warp Yarn Cost = (Fabric Length × EPI × Crimp% × Yarn Price) ÷ (840 × Yarn Count)
Weft Yarn Cost per Meter:
Weft Yarn Cost = (Fabric Width × PPI × Crimp% × Yarn Price) ÷ (840 × Yarn Count)
Let's consider an example to illustrate the calculation process:
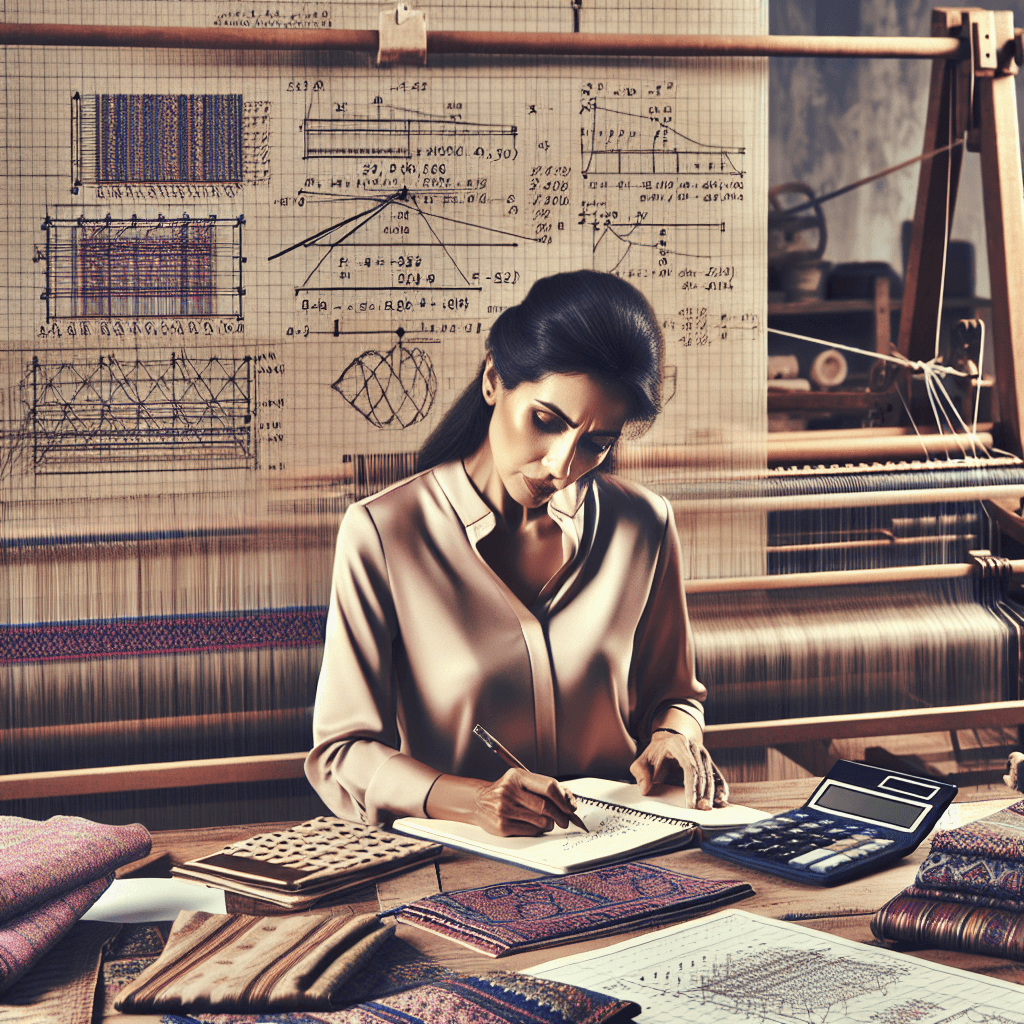
Suppose a textile business wants to estimate the yarn costs for a cotton fabric with the following parameters:
- Fabric Length: 100 meters
- Fabric Width: 1.5 meters
- Warp Yarn Count: 40s
- Weft Yarn Count: 40s
- EPI: 90
- PPI: 80
- Crimp Percentage: 5%
- Waste Percentage: 3%
- Yarn Price: $4.50 per kg
Using the provided formulas, the yarn costs can be calculated as follows:
Warp Yarn Cost per Meter:
Warp Yarn Cost = (100 × 90 × 1.05 × 4.50) ÷ (840 × 40) = $1.27
Weft Yarn Cost per Meter:
Weft Yarn Cost = (1.5 × 80 × 1.05 × 4.50) ÷ (840 × 40) = $0.17
By adding the warp and weft yarn costs, the total yarn cost per meter for this fabric would be $1.44. It's important to note that this is just one component of the overall fabric cost, and other factors such as sizing, weaving, dyeing, and finishing costs must also be considered.
By utilizing these formulas and carefully considering the various parameters involved, textile businesses can accurately estimate the yarn costs for their woven fabrics, ultimately contributing to a more comprehensive and reliable fabric cost estimation process.
Accounting for Sizing and Chemical Costs
In addition to yarn costs, textile businesses must also account for sizing and chemical costs when estimating the overall fabric cost. Sizing is a crucial process in fabric production that involves applying a protective coating to the warp yarns before weaving. This coating helps strengthen the yarns, reduce breakage, and improve the weaving efficiency. However, the sizing process also adds to the production expenses, and these costs must be carefully considered.
Sizing costs typically include expenses related to the following:
- Chemicals used in the sizing solution
- Power consumption during the sizing process
- Labor required to operate and maintain the sizing equipment
- Maintenance and repair costs for the sizing machinery
The specific sizing costs can vary based on factors such as the yarn count and quality. Finer yarns with higher counts often require more delicate handling and may incur higher sizing expenses. Additionally, the type and quality of the chemicals used in the sizing solution can impact the overall cost.
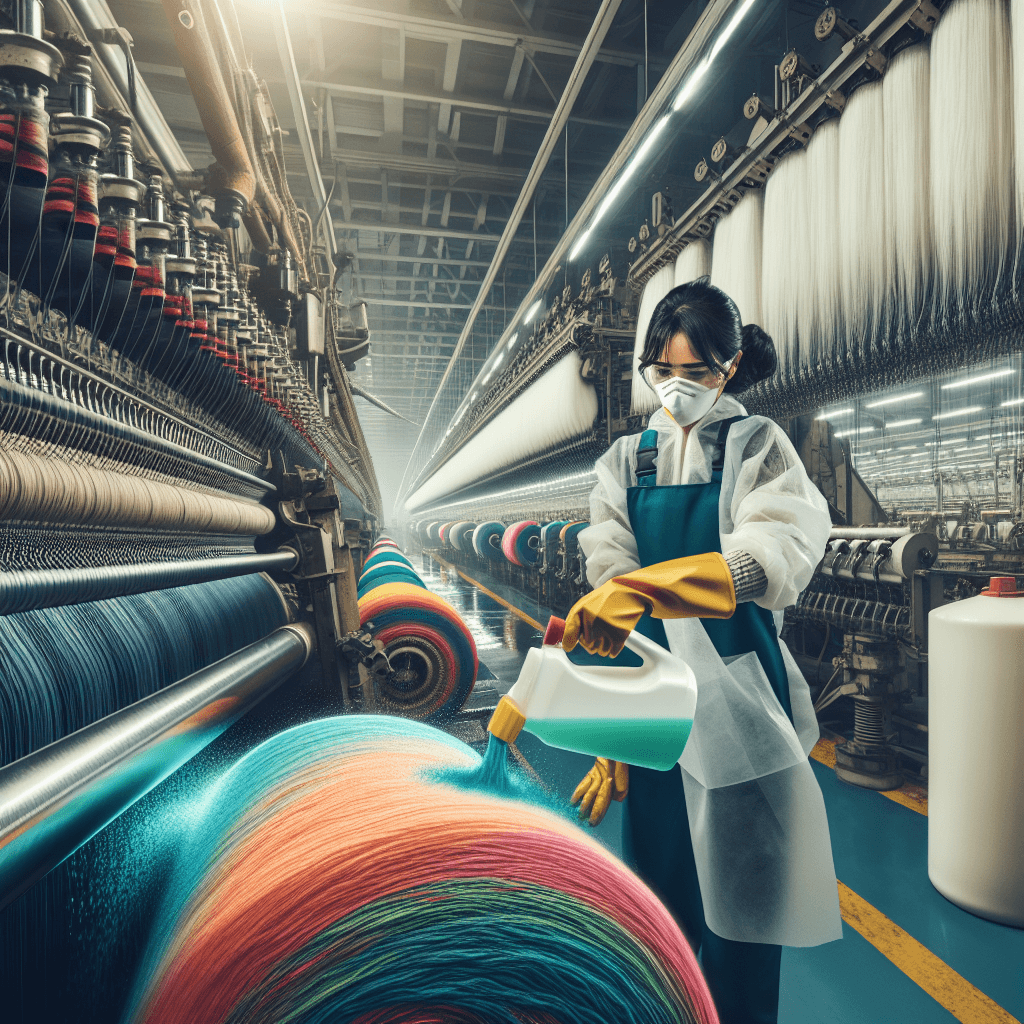
To estimate the sizing cost, textile businesses can use industry-standard benchmarks or calculate their own costs based on historical data. A typical sizing cost per kilogram of warp yarn can range from $0.15 to $0.30, depending on the specific requirements and processes involved.
For example, let's consider a fabric with a warp yarn count of 40s and a fabric length of 100 meters. If the sizing cost per kilogram of warp yarn is $0.20, and the warp yarn weight is 1.5 kilograms per 100 meters, the sizing cost per meter can be calculated as follows:
Sizing Cost per Meter = (Warp Yarn Weight per 100 Meters × Sizing Cost per Kilogram) ÷ Fabric Length
Sizing Cost per Meter = (1.5 × 0.20) ÷ 100 = $0.003
In this case, the sizing cost per meter of fabric would be $0.003.
It's important to note that sizing costs can also be expressed in terms of cost per meter of fabric, taking into account the fabric width. For instance, if the fabric width is 1.5 meters and the sizing cost per meter of fabric length is $0.003, the sizing cost per square meter of fabric would be $0.002.
By accurately accounting for sizing and chemical costs, textile businesses can gain a more comprehensive understanding of their production expenses and make informed decisions when estimating the overall fabric cost. This information is crucial for setting competitive prices, optimizing production processes, and ensuring the profitability of their operations.
Estimating Weaving Costs Based on Loom Type
Another significant component of fabric cost estimation is determining the weaving costs based on the type of loom used in the production process. Weaving is the critical step where the warp and weft yarns are interlaced to create the fabric structure. The cost of weaving can vary depending on several factors, including the type of loom, the complexity of the fabric design, and the efficiency of the weaving process.
When estimating weaving costs, textile businesses must consider the following expenses:
- Power consumption during the weaving process
- Manpower required to operate and supervise the looms
- Maintenance and repair costs for the weaving machinery
- Depreciation of the weaving equipment over time
The type of loom used in the production process can significantly impact the weaving costs. There are two main categories of looms: mill-made looms and powerlooms.
-
Mill-Made Looms: These are sophisticated, automated looms typically found in large-scale textile mills. They are designed for high-speed, continuous fabric production and can handle complex weave patterns. Mill-made looms generally have higher production rates and lower labor requirements compared to powerlooms. However, they also have higher capital costs and maintenance expenses.
-
Powerlooms: Powerlooms are semi-automatic or manual looms commonly used in smaller-scale textile operations. They have lower production speeds and may require more manual intervention compared to mill-made looms. Powerlooms are less expensive to purchase and maintain but have higher labor costs due to the need for skilled operators.
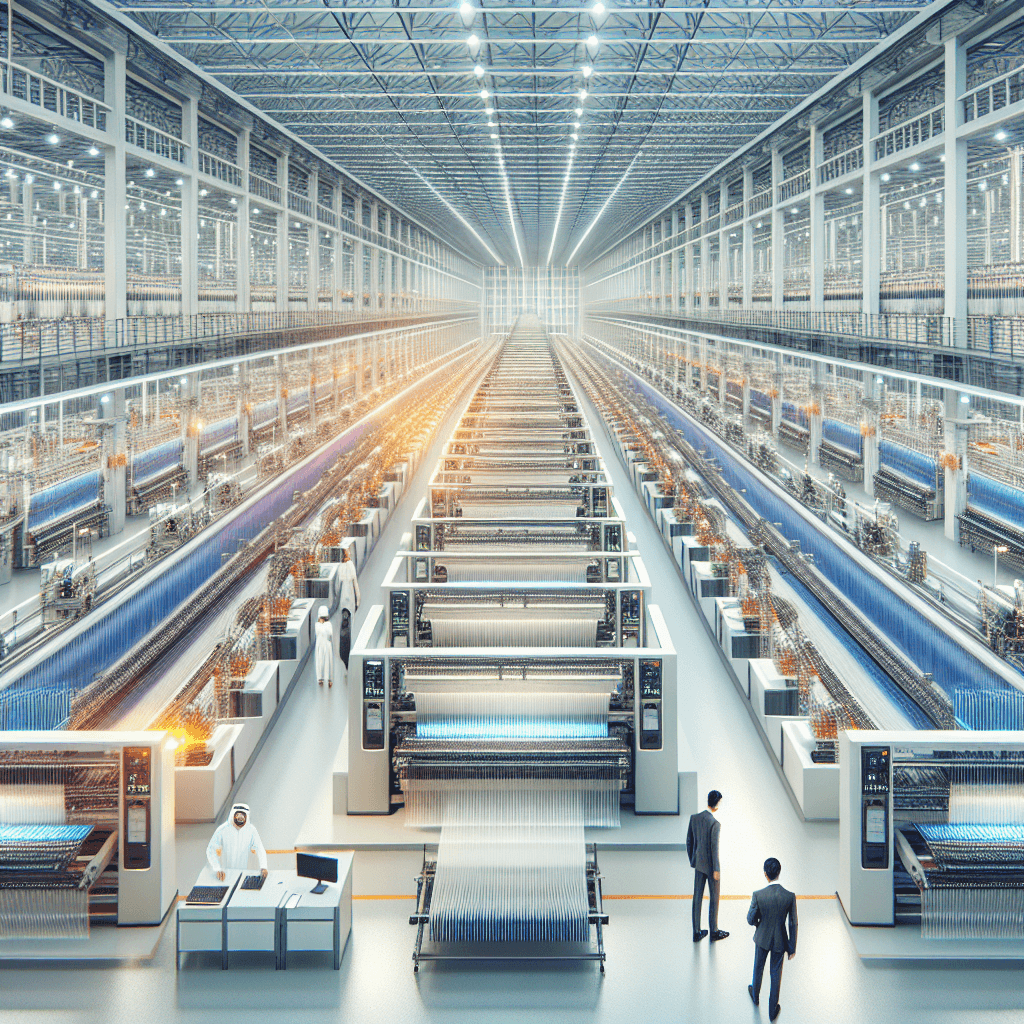
To calculate the weaving cost per meter of fabric, textile businesses can use the following formula:
Weaving Cost per Meter = (Power Cost + Labor Cost + Maintenance Cost + Depreciation Cost) ÷ Fabric Length
For example, let's consider a fabric with a length of 100 meters woven on a mill-made loom. If the power cost is $0.05 per meter, the labor cost is $0.10 per meter, the maintenance cost is $0.03 per meter, and the depreciation cost is $0.02 per meter, the weaving cost per meter can be calculated as follows:
Weaving Cost per Meter = (0.05 + 0.10 + 0.03 + 0.02) ÷ 100 = $0.002
In this case, the weaving cost per meter of fabric would be $0.002.
Another way to express weaving costs is by calculating the cost per pick inserted. A pick refers to a single weft yarn inserted across the fabric width. The number of picks per inch (PPI) is a crucial factor in determining the fabric density and weaving efficiency. To calculate the weaving cost per pick, textile businesses can use the following formula:
Weaving Cost per Pick = Weaving Cost per Meter ÷ (PPI × Fabric Width)
Using the previous example, if the fabric has a PPI of 80 and a width of 1.5 meters, the weaving cost per pick would be:
Weaving Cost per Pick = 0.002 ÷ (80 × 1.5) = $0.0000167
By accurately estimating weaving costs based on loom type and considering factors such as power consumption, labor, maintenance, and depreciation, textile businesses can gain a clearer understanding of their production expenses. This information is vital for making informed pricing decisions, optimizing production processes, and ensuring the overall profitability of their operations.
Dyeing and Finishing: Key Cost Considerations
Dyeing and finishing processes play a crucial role in transforming raw fabric into the final product desired by customers. These processes not only enhance the aesthetic appeal of the fabric but also impart various functional properties. However, dyeing and finishing also contribute significantly to the overall fabric cost, and textile businesses must carefully consider the associated expenses when estimating the total cost of production.
Dyeing costs can vary depending on several factors, including:
- Fabric dimensions (length and width)
- Desired shade or color intensity
- Dye class (reactive, disperse, vat, etc.)
- Metamerism requirements (color consistency under different lighting conditions)
The complexity of the dyeing process and the type of dye used can greatly impact the overall cost. For example, achieving a deep, rich shade may require higher dye concentrations and longer processing times compared to lighter shades. Additionally, certain dye classes, such as reactive dyes for cellulosic fibers, may have higher costs compared to other dye types.

Finishing processes, such as softening, special treatments, and functional coatings, also add to the total fabric cost. These processes enhance the fabric's performance, durability, and market appeal but require additional resources and specialized equipment. Some common finishing processes and their associated costs include:
Finishing Process | Description | Approximate Cost Range |
---|---|---|
Softening | Improves fabric hand feel and drape | $0.05 - $0.15 per meter |
Water-Repellent Coating | Imparts water resistance to the fabric | $0.10 - $0.30 per meter |
Antimicrobial Treatment | Prevents growth of bacteria and fungi | $0.15 - $0.40 per meter |
Flame-Retardant Finishing | Reduces fabric flammability | $0.20 - $0.50 per meter |
When estimating dyeing and finishing costs, textile businesses must also consider the desired level of color fastness and washability. Higher color fastness requirements, such as resistance to fading under sunlight or multiple wash cycles, may necessitate the use of more expensive dyes and additional processing steps, ultimately increasing the overall cost.
Fabric shrinkage is another critical factor to consider during dyeing and finishing. Most fabrics undergo some degree of shrinkage during these processes, and textile businesses must account for this loss when calculating the final fabric cost. Shrinkage can vary depending on the fiber type, fabric construction, and processing conditions, but a typical range is between 2% to 5%.
To estimate the dyeing and finishing cost per meter of fabric, textile businesses can use the following formula:
Dyeing and Finishing Cost per Meter = (Dyeing Cost + Finishing Cost) × (1 + Shrinkage Percentage)
For example, if the dyeing cost is $0.50 per meter, the finishing cost is $0.20 per meter, and the expected shrinkage is 3%, the total dyeing and finishing cost per meter would be:
Dyeing and Finishing Cost per Meter = (0.50 + 0.20) × (1 + 0.03) = $0.721
By carefully considering the various factors that influence dyeing and finishing costs, such as shade complexity, dye class, finishing treatments, color fastness requirements, and shrinkage, textile businesses can accurately estimate this crucial component of the total fabric cost. This information is essential for making informed pricing decisions, optimizing production processes, and maintaining profitability in a competitive market.
Planning for Fabric Wastage and Shrinkage Losses
In the textile industry, fabric wastage and shrinkage are inevitable challenges that can significantly impact the overall cost of production. Textile businesses must account for these losses when estimating the total fabric cost to ensure accurate pricing and maintain profitability. By understanding the typical wastage and shrinkage rates and incorporating them into the cost calculation process, companies can make informed decisions and minimize the financial impact of these losses.
Fabric wastage occurs at various stages of the production process, from weaving to cutting and sewing. Some common sources of fabric wastage include:
- Loom setup and adjustment losses
- Selvedge wastage during weaving
- Cutting room losses due to pattern matching and nesting inefficiencies
- End-of-roll wastage and remnants
On average, textile businesses can expect a wastage rate of 2-3% during the weaving process. This means that for every 100 meters of fabric woven, approximately 2-3 meters may be lost due to various factors such as loom setup, selvedge trimming, and quality issues.
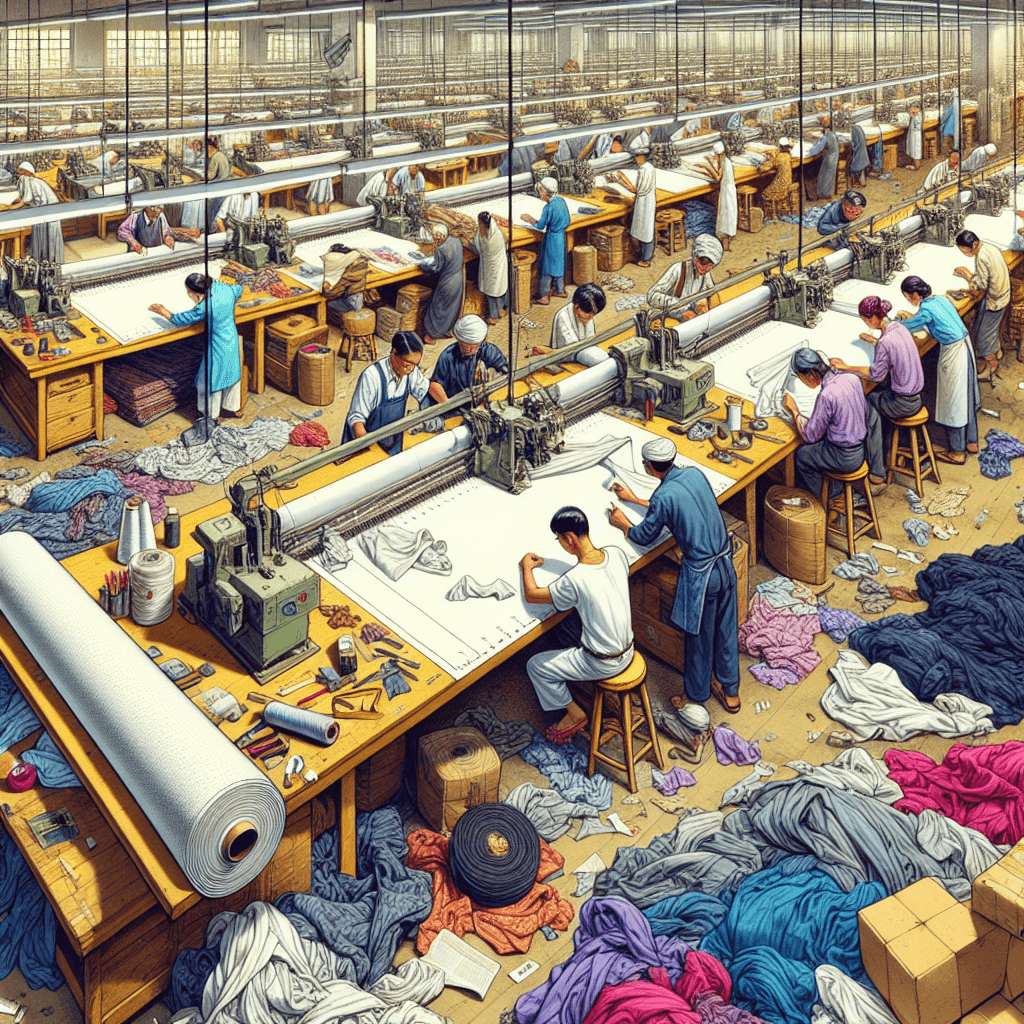
Shrinkage is another critical factor that textile businesses must consider when planning for fabric usage and costing. Most fabrics undergo some degree of shrinkage during the dyeing and finishing processes, as well as during subsequent washing and drying cycles. The amount of shrinkage can vary depending on the fiber type, fabric construction, and processing conditions.
Typical shrinkage rates for common fabric types include:
- Cotton: 3-5%
- Linen: 4-6%
- Wool: 2-4%
- Polyester: 1-2%
- Nylon: 1-2%
To account for shrinkage, textile businesses must order additional fabric to ensure they have sufficient material to meet their production requirements. For example, if a company needs 1000 meters of finished fabric and anticipates a 4% shrinkage rate, they would need to order approximately 1041 meters of raw fabric to compensate for the expected loss.
Fabric wastage and shrinkage not only impact the amount of material required but also directly affect the overall fabric cost. Textile businesses must factor in these losses when calculating the total cost of production. A typical wastage and shrinkage combined loss can account for around 5-7% of the total fabric cost.
To illustrate the impact of wastage and shrinkage on fabric cost, consider the following example:
Fabric Type | Quantity Required (m) | Wastage Rate | Shrinkage Rate | Total Fabric Needed (m) | Fabric Cost per Meter | Total Fabric Cost |
---|---|---|---|---|---|---|
Cotton | 1000 | 3% | 4% | 1074 | $5.00 | $5,370 |
In this scenario, the textile business needs 1000 meters of finished cotton fabric. To account for the expected 3% wastage and 4% shrinkage, they must order 1074 meters of raw fabric. With a fabric cost of $5.00 per meter, the total fabric cost, including wastage and shrinkage, would be $5,370.
By accurately planning for fabric wastage and shrinkage losses, textile businesses can minimize the financial impact of these challenges. This involves carefully monitoring wastage rates, implementing efficient cutting and nesting techniques, and working closely with suppliers to ensure consistent fabric quality and shrinkage performance. By incorporating these considerations into the fabric costing process, companies can make informed pricing decisions, optimize their production processes, and maintain a competitive edge in the market.
Putting It All Together: Calculating Total Fabric Cost
Estimating the total fabric cost is a critical task for textile businesses, as it directly impacts pricing strategies, profitability, and competitiveness in the market. To accurately calculate the total fabric cost, companies must consider all the various components that contribute to the final expense. This includes the costs associated with raw materials, dyeing, finishing, wastage, and shrinkage.
The total fabric cost can be broken down into two main categories:
-
Direct Costs: These are expenses directly related to the production of the fabric, such as:
- Raw material costs (e.g., yarns, fibers)
- Dyestuffs and chemicals used in dyeing and finishing
- Labor costs for production processes
- Energy and utility costs for running machinery
-
Indirect Costs: These are expenses that are not directly tied to the production process but still impact the overall cost, such as:
- Overhead costs (e.g., rent, insurance, administrative expenses)
- Depreciation of machinery and equipment
- Research and development expenses
- Marketing and sales costs
To calculate the total fabric cost per meter, textile businesses can use the following formula:
Total Fabric Cost per Meter = Direct Costs per Meter + Indirect Costs per Meter
The direct costs per meter can be further broken down as follows:
Direct Costs per Meter = Greige Fabric Cost per Meter + Dyeing Cost per Meter + Finishing Cost per Meter + Wastage Cost per Meter + Shrinkage Cost per Meter
Indirect costs are typically allocated to the fabric cost based on a predetermined overhead rate, which is calculated by dividing the total indirect costs by the total production volume.
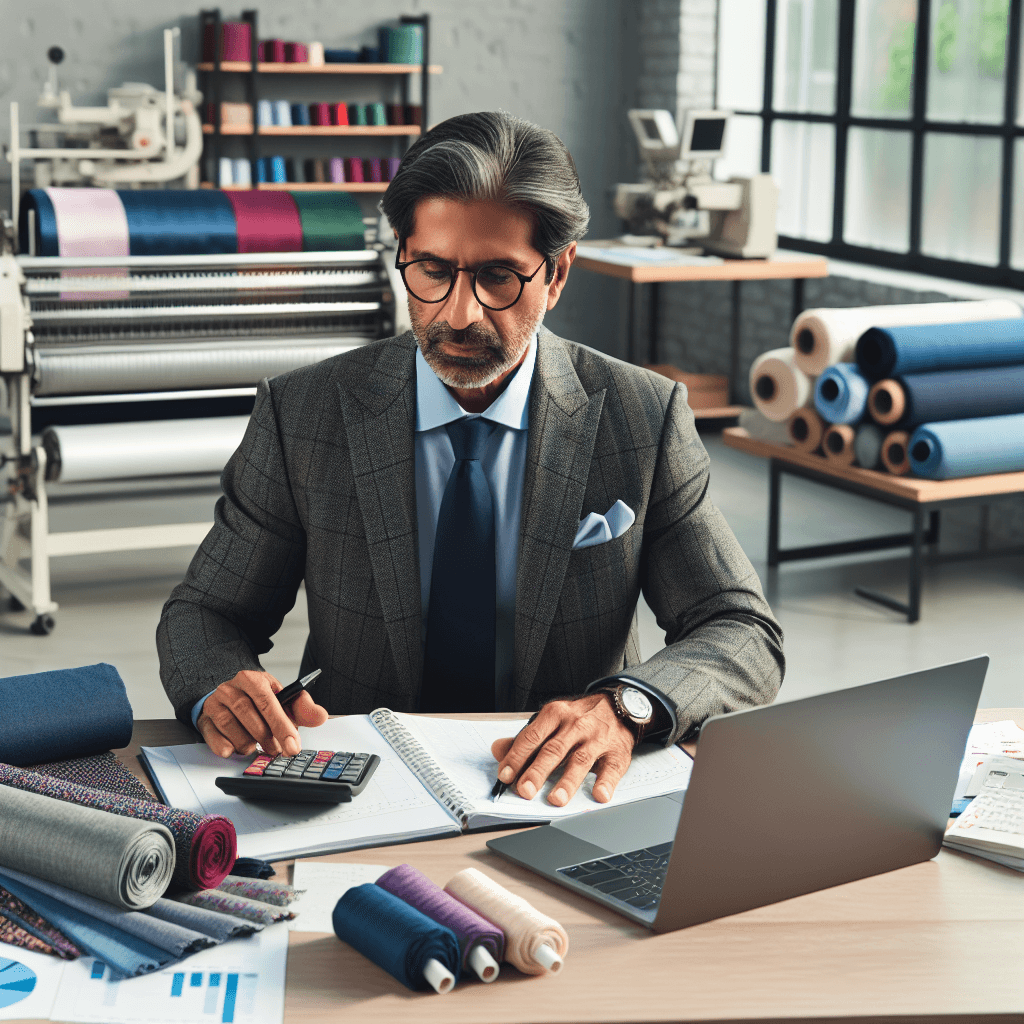
Let's consider an example to illustrate the total fabric cost calculation:
Cost Component | Cost per Meter |
---|---|
Greige Fabric Cost | $3.50 |
Dyeing Cost | $0.75 |
Finishing Cost | $0.50 |
Wastage Cost (3%) | $0.11 |
Shrinkage Cost (4%) | $0.14 |
Direct Costs per Meter | $5.00 |
Indirect Costs per Meter (20% overhead rate) | $1.00 |
Total Fabric Cost per Meter | $6.00 |
In this example, the direct costs per meter, including the greige fabric cost, dyeing, finishing, wastage, and shrinkage, amount to $5.00. The indirect costs, calculated using a 20% overhead rate, add an additional $1.00 per meter. Therefore, the total fabric cost per meter is $6.00.
It's important to note that the total fabric cost should also include a target profit margin to ensure the long-term sustainability and growth of the business. Typical profit margins in the textile industry range from 10% to 20%, depending on factors such as market conditions, competition, and product positioning.
By accurately calculating the total fabric cost, textile businesses can make informed decisions regarding pricing, profitability, and resource allocation. This information is crucial for setting competitive prices, negotiating with customers, and optimizing production processes to maximize efficiency and minimize waste. By regularly reviewing and updating fabric cost calculations, companies can stay ahead of market trends, adapt to changing conditions, and maintain a strong position in the industry.
Conclusion
In today's competitive textile industry, accurately estimating fabric costs is essential for businesses looking to optimize their operations, improve profitability, and deliver high-quality products to their customers. By understanding the key factors that influence fabric costs, such as raw material prices, yarn counts, fabric weight, and processing expenses, companies can make informed decisions and stay ahead of the curve.
Throughout this comprehensive guide, we have explored the various components that contribute to the total fabric cost, including:
- The importance of yarn costs and how to calculate them for woven fabrics
- Accounting for sizing and chemical costs in the production process
- Estimating weaving costs based on loom type and efficiency
- Considering dyeing and finishing expenses, including shade complexity and special treatments
- Planning for fabric wastage and shrinkage losses to minimize financial impact
By breaking down each component and providing practical examples and formulas, this guide aims to empower textile businesses with the knowledge and tools needed to accurately estimate fabric costs and make data-driven decisions.
Implementing a fabric cost estimator can revolutionize the way textile businesses operate, enabling them to:
- Streamline the costing process and generate quick, accurate estimates
- Improve customer satisfaction by providing transparent and competitive pricing
- Optimize inventory management and production planning
- Identify areas for cost savings and process improvements
- Enhance profitability and maintain a competitive edge in the market
To take your textile business to the next level, consider integrating a fabric cost estimator into your website or internal systems. By leveraging the power of automation and data-driven insights, you can transform your costing process, improve efficiency, and drive long-term success.
Don't let manual calculations and guesswork hold you back. Embrace the future of fabric costing and unlock the full potential of your textile business. Explore the benefits of a fabric cost estimator today and take the first step towards optimizing your operations and achieving your growth objectives.
Remember, in the fast-paced world of textiles, those who adapt and innovate will thrive. By staying informed, embracing technology, and making data-driven decisions, you can position your business for success and navigate the challenges of an ever-evolving industry.