Labor cost is a critical financial metric that represents the total amount of money a business spends on its workforce. It encompasses all expenses associated with employing staff, including wages, salaries, benefits, taxes, and other related costs. Understanding labor costs is essential for businesses of all sizes, as it directly impacts profitability, budgeting, and overall financial health.
The primary components of labor cost include:
- Direct wages and salaries: The base pay provided to employees for their work
- Overtime pay: Additional compensation for hours worked beyond the standard workweek
- Payroll taxes: Employer-paid taxes, such as Social Security, Medicare, and unemployment taxes
- Employee benefits: Health insurance, retirement plans, paid time off, and other fringe benefits
- Training and development expenses: Costs associated with onboarding, upskilling, and professional development
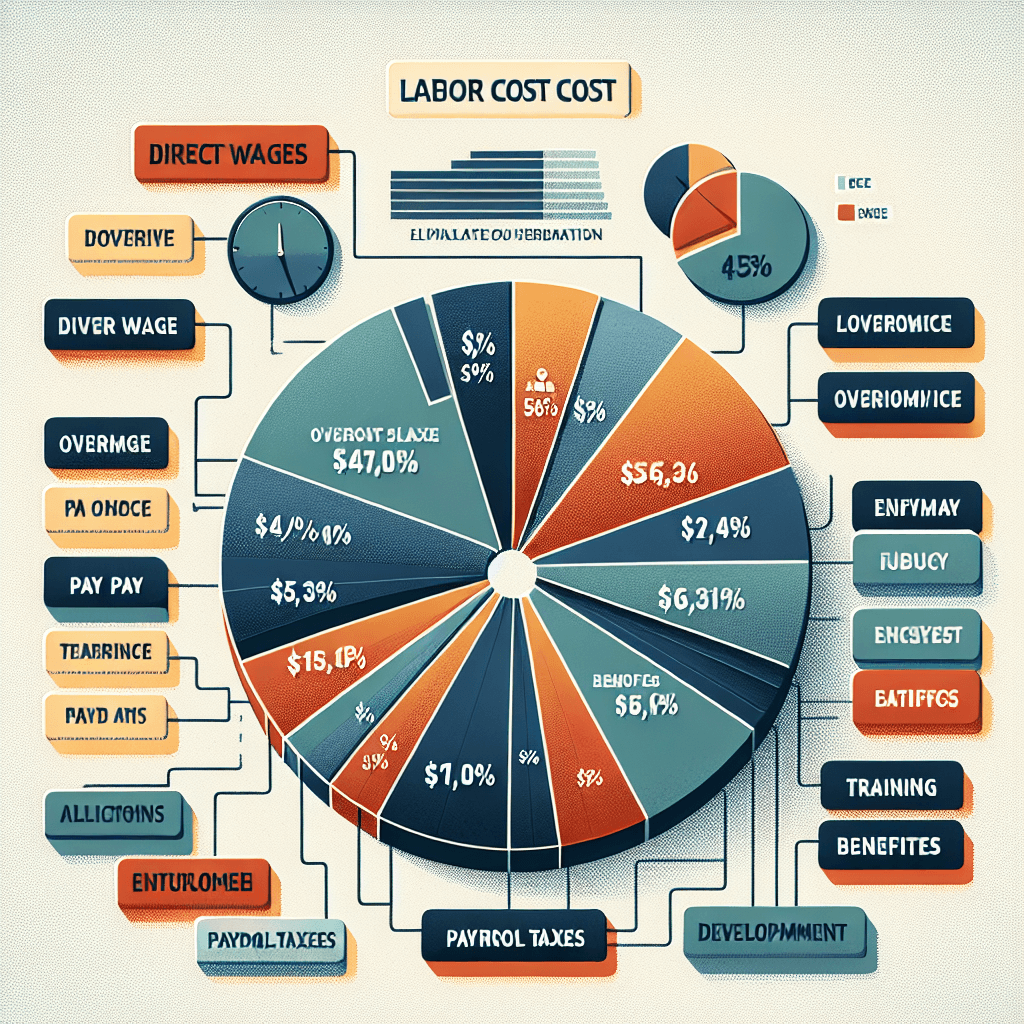
Accurately calculating and monitoring labor costs enables businesses to make informed decisions regarding staffing, pricing, and resource allocation. By understanding the true cost of their workforce, companies can identify areas for optimization, streamline processes, and develop strategies to enhance overall profitability.
Moreover, having a clear picture of labor costs is crucial for creating realistic budgets, forecasting future expenses, and ensuring compliance with labor laws and regulations. In the following sections, we will delve into the various methods for calculating labor costs, including hourly, annual, and project-based approaches, as well as explore strategies for managing and optimizing these expenses.
According to the ILOSTAT, labor costs are critical for assessing the competitiveness of enterprises and countries, particularly in the manufacturing sector. The mean nominal hourly labor cost per employee by economic activity is a key indicator for comparisons across countries and industries, updated annually as part of the Competitiveness Indicators database (ILOSTAT).
Additionally, a detailed breakdown of employee compensation costs, including wages, salaries, and benefits across various industries and occupations, is provided by MployerAdvisor. This analysis helps businesses understand the distribution of total labor costs between direct wages and supplementary benefits, offering tools like custom benefits reports and insurance comparisons to aid in compensation strategy decisions (MployerAdvisor).
How to Calculate Labor Cost per Hour
Calculating labor cost per hour is a fundamental skill for businesses, as it helps determine the true cost of an employee's time and ensures accurate pricing, budgeting, and resource allocation. To calculate the hourly labor cost, use the following formula:
Hourly Labor Cost = (Total Annual Employee Cost) ÷ (Total Annual Hours Worked)
When determining the total annual employee cost, consider the following factors:
- Gross wages: The employee's base hourly rate multiplied by the total hours worked in a year
- Payroll taxes: Employer-paid taxes, such as Social Security, Medicare, and unemployment taxes
- Employee benefits: Health insurance, retirement plans, paid time off, and other fringe benefits
- Overhead costs: Expenses such as office space, equipment, and utilities allocated to the employee
To calculate the total annual hours worked, multiply the number of hours worked per week by the number of weeks in a year (typically 52), subtracting any paid time off, such as vacation days or holidays.
For example, let's calculate the hourly labor cost for an employee with the following details:
- Gross annual wages: $50,000
- Payroll taxes: $4,000
- Employee benefits: $6,000
- Overhead costs: $5,000
- Hours worked per week: 40
- Paid time off: 2 weeks (80 hours)
Total Annual Employee Cost = $50,000 + $4,000 + $6,000 + $5,000 = $65,000 Total Annual Hours Worked = (40 hours × 50 weeks) = 2,000 hours
Hourly Labor Cost = $65,000 ÷ 2,000 hours = $32.50 per hour
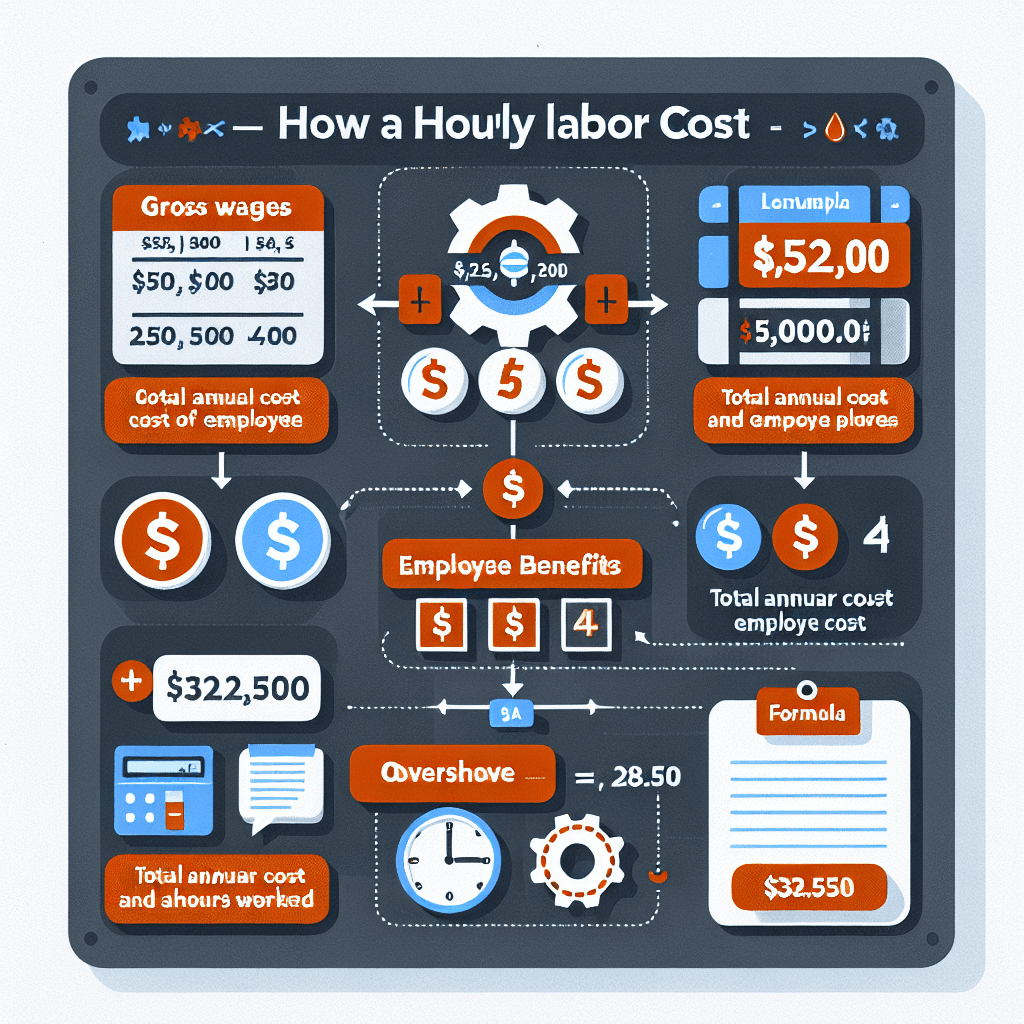
By accurately calculating the hourly labor cost, businesses can make informed decisions about pricing, staffing, and resource allocation. This information is particularly useful when bidding on projects, creating budgets, or comparing the cost-effectiveness of different staffing options (e.g., full-time employees vs. contractors).
Calculating Annual Labor Costs
Annual labor costs represent the total amount a business spends on its workforce over the course of a year. Accurately calculating annual labor costs is crucial for budgeting, financial planning, and assessing the overall profitability of a company. To calculate annual labor costs, use the following formula:
Annual Labor Cost = (Total Annual Employee Costs) × (Number of Employees)
When calculating the total annual employee costs, it's essential to include all relevant expenses:
- Gross wages or salaries: The base pay provided to employees for their work
- Payroll taxes: Employer-paid taxes, such as Social Security, Medicare, and unemployment taxes
- Employee benefits: Health insurance, retirement plans, paid time off, and other fringe benefits
- Overtime pay: Additional compensation for hours worked beyond the standard workweek
- Training and development expenses: Costs associated with onboarding, upskilling, and professional development
- Overhead costs: Expenses such as office space, equipment, and utilities allocated to the employee
Here's an example of calculating annual labor costs for a business with 50 employees:
Expense Category | Annual Cost per Employee |
---|---|
Gross wages | $50,000 |
Payroll taxes | $4,000 |
Employee benefits | $6,000 |
Overtime pay | $2,000 |
Training expenses | $1,000 |
Overhead costs | $5,000 |
Total Annual Employee Cost | $68,000 |
Annual Labor Cost = $68,000 × 50 employees = $3,400,000
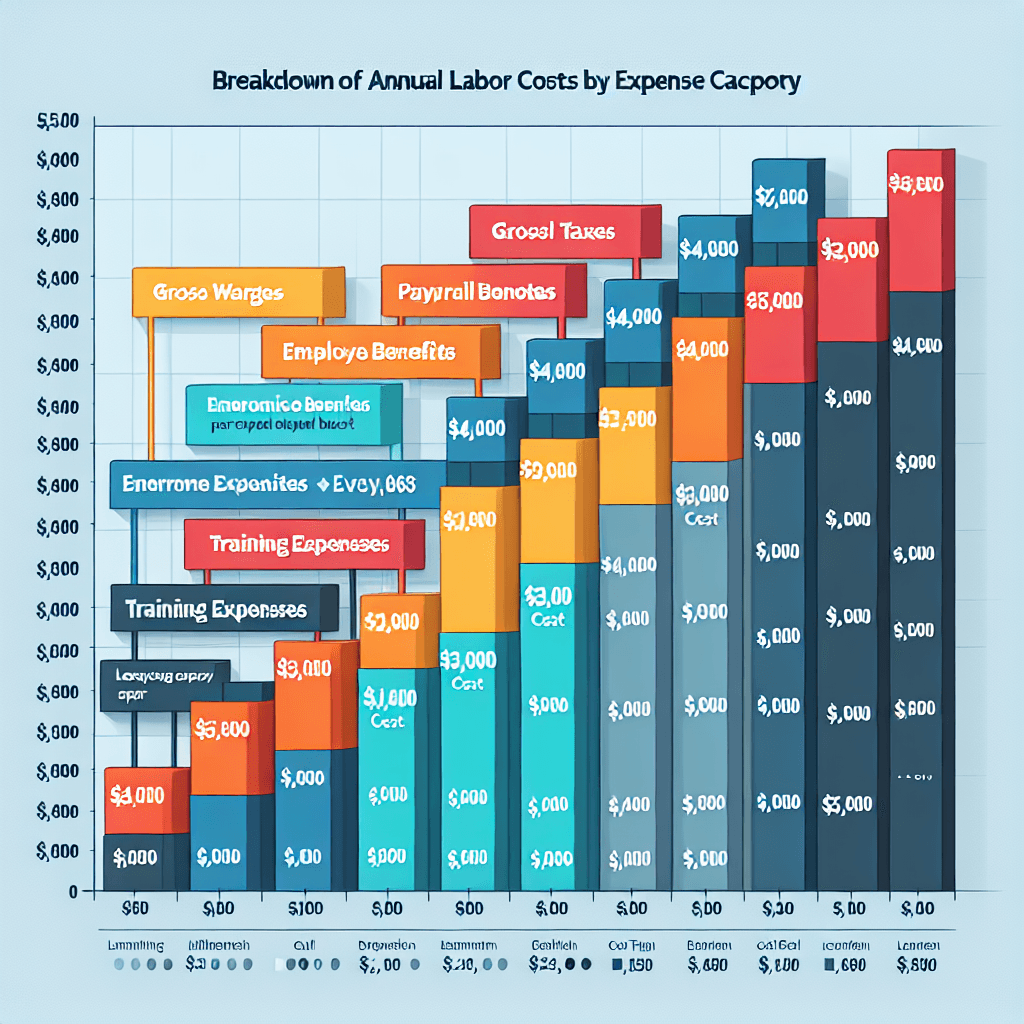
By accurately calculating annual labor costs, businesses can:
- Create realistic budgets and financial projections
- Identify areas for cost optimization and efficiency improvements
- Make informed decisions about staffing levels, compensation, and benefits
- Assess the financial impact of hiring additional employees or implementing workforce changes
- Ensure compliance with labor laws and regulations
Regularly reviewing and updating annual labor cost calculations is essential to maintain accurate financial records and make data-driven decisions that support the long-term success of the business.
Determining Project Labor Costs
Accurately estimating project labor costs is essential for businesses to ensure profitability, create competitive bids, and manage resources effectively. When calculating project labor costs, consider the following factors:
- Project scope and duration: Clearly define the tasks, deliverables, and timeline of the project
- Required skills and expertise: Identify the specific skills and experience levels needed for the project
- Number of employees involved: Determine the number of team members required to complete the project successfully
- Hourly labor rates: Use the calculated hourly labor cost for each employee (refer to the previous section on calculating hourly labor costs)
- Estimated hours per task: Break down the project into individual tasks and estimate the number of hours needed for each task
To calculate the total project labor cost, use this formula:
Total Project Labor Cost = ∑ (Hourly Labor Cost × Estimated Hours) for each employee
Here's an example of calculating project labor costs for a web development project:
Task | Employee | Hourly Rate | Estimated Hours | Task Labor Cost |
---|---|---|---|---|
Design | Employee A | $50 | 40 | $2,000 |
Front-end Development | Employee B | $60 | 80 | $4,800 |
Back-end Development | Employee C | $70 | 120 | $8,400 |
Testing & QA | Employee D | $40 | 20 | $800 |
Project Management | Employee E | $80 | 30 | $2,400 |
Total Project Labor Cost | $18,400 |
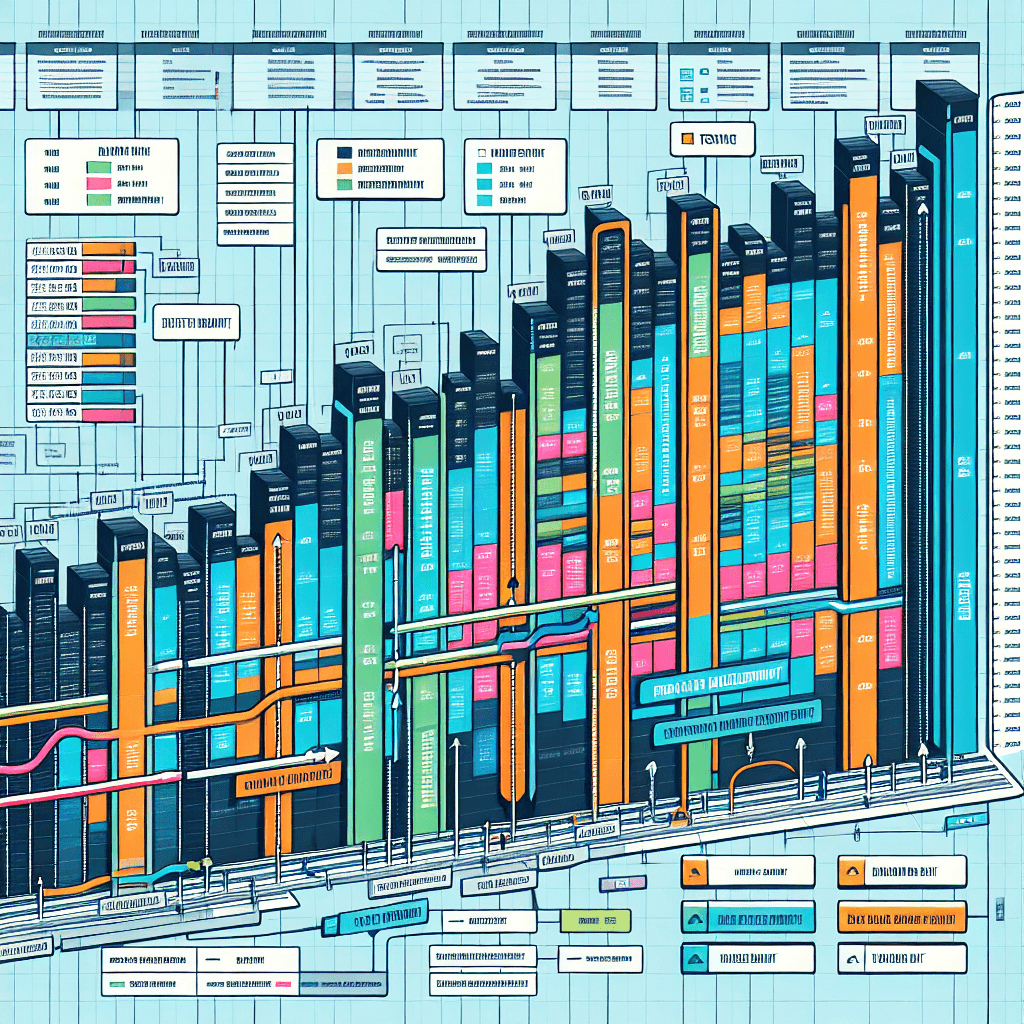
Tips for accurately tracking project labor expenses:
- Use time tracking software to monitor employee hours spent on each task
- Regularly review and update project estimates based on actual time spent
- Account for potential delays, revisions, or scope changes that may impact labor costs
- Communicate project progress and labor costs to stakeholders and clients regularly
By accurately determining project labor costs, businesses can:
- Create realistic project budgets and pricing
- Optimize resource allocation and team utilization
- Identify areas for process improvement and efficiency gains
- Make informed decisions about project profitability and feasibility
- Improve project planning and estimation skills over time
Effective project labor cost management is crucial for delivering successful projects, maintaining client satisfaction, and ensuring the long-term profitability of the business.
Understanding Labor Cost Percentage
Labor cost percentage is a key metric that represents the proportion of a company's revenue that is spent on employee wages, benefits, and other labor-related expenses. This percentage helps businesses assess their financial health, efficiency, and profitability. To calculate the labor cost percentage, use the following formula:
Labor Cost Percentage = (Total Labor Costs ÷ Total Revenue) × 100
For example, if a restaurant has total annual labor costs of $500,000 and generates $1,500,000 in revenue, the labor cost percentage would be:
Labor Cost Percentage = ($500,000 ÷ $1,500,000) × 100 = 33.33%
Ideal labor cost percentage ranges vary by industry, as some sectors are more labor-intensive than others. Here are some general guidelines:
Industry | Ideal Labor Cost Percentage Range |
---|---|
Restaurants | 25% - 35% |
Retail | 10% - 20% |
Manufacturing | 20% - 30% |
Construction | 20% - 40% |
Healthcare | 50% - 60% |
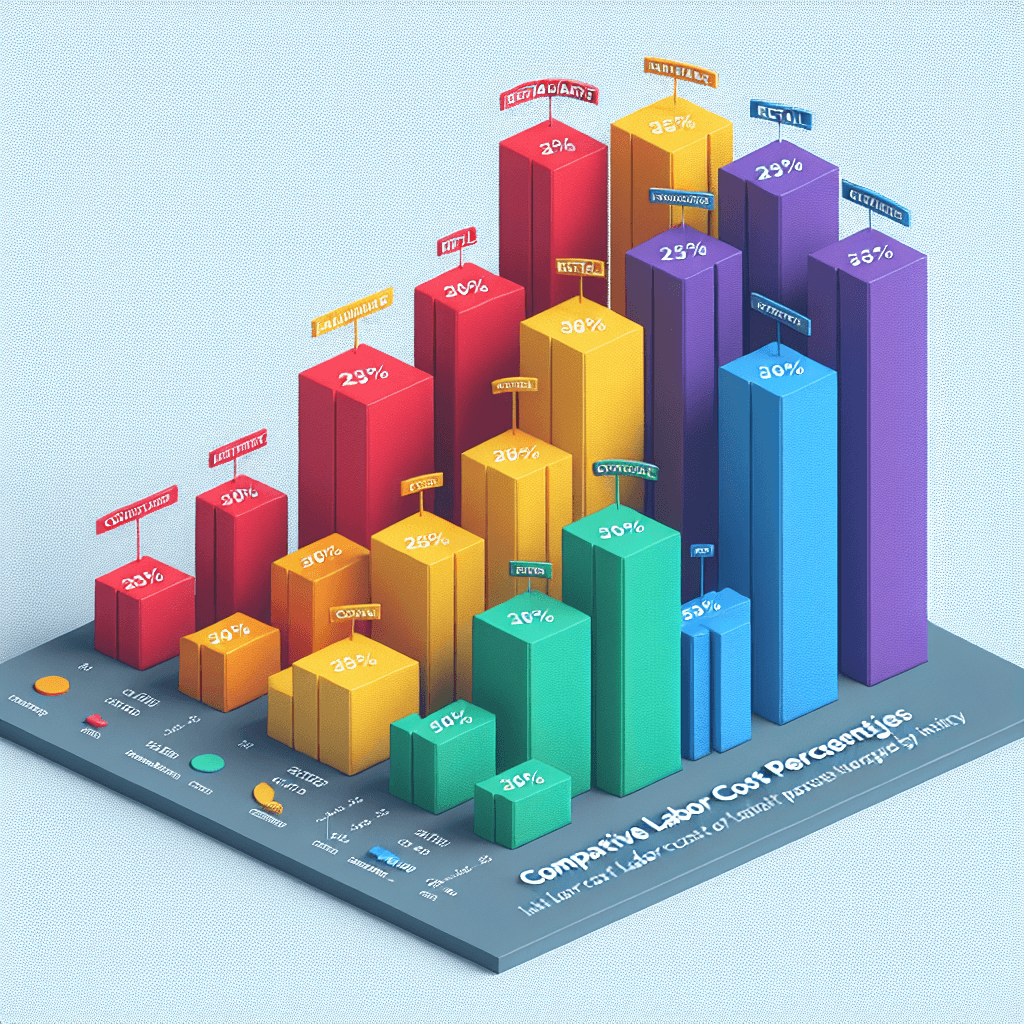
Monitoring and managing labor cost percentage is crucial for several reasons:
- Profitability: High labor cost percentages can erode profit margins and impact the overall financial health of the business
- Efficiency: Analyzing labor cost percentages can help identify areas for process improvement, automation, or workforce optimization
- Budgeting: Understanding labor cost percentages enables businesses to create accurate budgets and financial projections
- Benchmarking: Comparing labor cost percentages to industry standards or competitors can provide insights into a company's relative performance and competitiveness
To optimize labor cost percentage, consider the following strategies:
- Implement efficient scheduling and resource allocation practices
- Invest in training and development to improve employee productivity
- Automate processes and tasks where possible to reduce labor costs
- Regularly review and adjust staffing levels based on business needs
- Negotiate better rates for employee benefits and insurance plans
By effectively managing labor cost percentage, businesses can improve their financial performance, remain competitive in their industry, and make data-driven decisions that support long-term growth and success.
Direct vs. Indirect Labor Costs
Understanding the difference between direct and indirect labor costs is essential for accurately tracking, allocating, and managing labor expenses within a business. This distinction helps companies make informed decisions about pricing, budgeting, and resource allocation.
Direct Labor Costs: Direct labor costs are expenses directly associated with the production of goods or the delivery of services. These costs can be easily traced to specific products, projects, or tasks. Examples of direct labor costs include:
- Wages paid to assembly line workers in a manufacturing plant
- Salaries of construction workers building a house
- Hourly pay for a consultant working on a specific client project
- Compensation for a graphic designer creating a logo for a customer
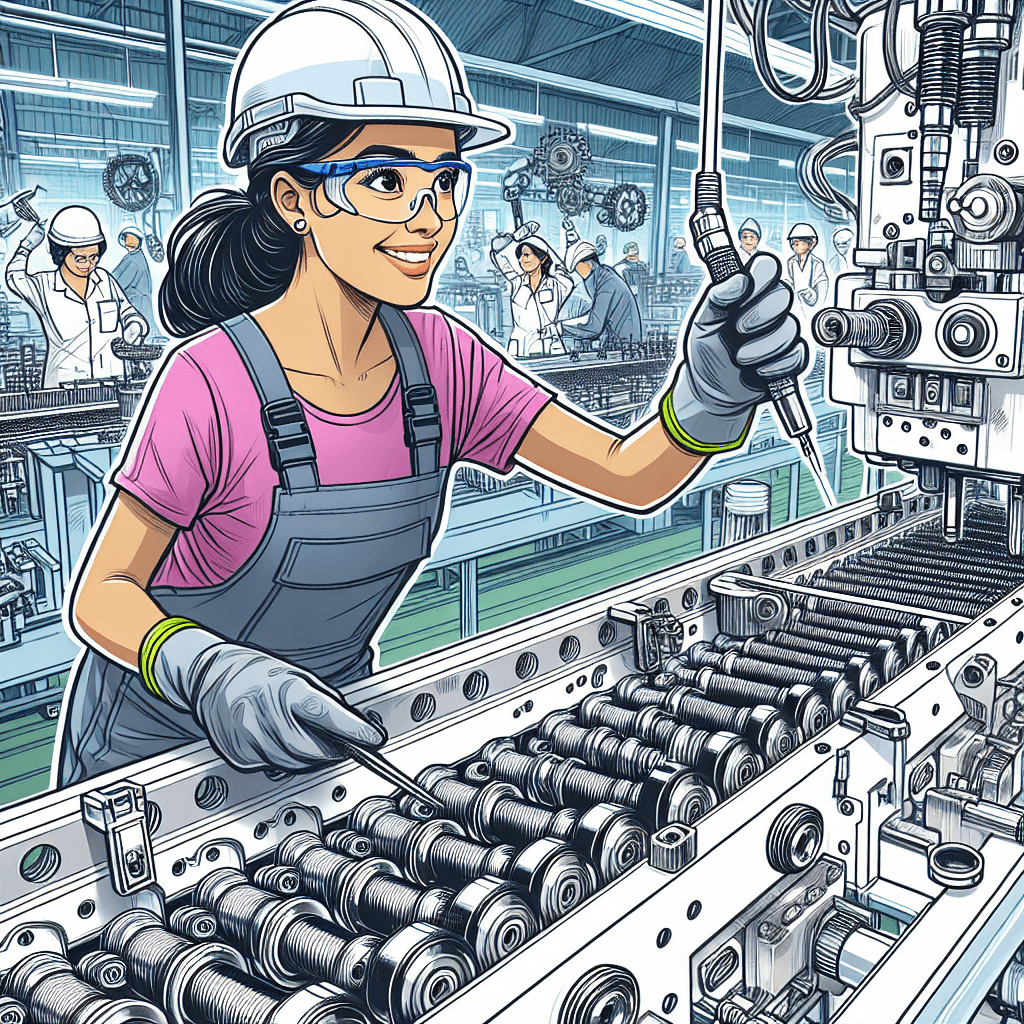
Indirect Labor Costs: Indirect labor costs are expenses that support the overall functioning of the business but cannot be directly attributed to a specific product, project, or task. These costs are often referred to as overhead expenses. Examples of indirect labor costs include:
- Salaries of administrative staff, such as HR personnel or office managers
- Wages paid to maintenance and janitorial staff
- Compensation for supervisors or managers overseeing multiple projects or departments
- Salaries of IT support staff maintaining company-wide systems and infrastructure
Accurately categorizing labor costs as direct or indirect is crucial for several reasons:
- Cost allocation: Proper classification ensures that labor expenses are allocated to the appropriate products, projects, or departments for accurate financial reporting and decision-making
- Pricing and bidding: Understanding the true cost of direct labor helps businesses set competitive prices and create accurate bids for projects or services
- Profitability analysis: Separating direct and indirect labor costs enables companies to assess the profitability of individual products, projects, or services
- Budgeting and forecasting: Accurate categorization of labor costs improves the precision of financial budgets and forecasts, enabling better resource planning and allocation
To effectively manage direct and indirect labor costs, businesses should:
- Implement time tracking systems to monitor employee hours and allocate them to specific projects or tasks
- Regularly review and update labor cost classifications to ensure accuracy
- Analyze the ratio of direct to indirect labor costs to identify areas for optimization and efficiency improvements
- Use cost allocation methods, such as activity-based costing, to assign indirect labor costs to products or services based on their consumption of resources
By accurately distinguishing between direct and indirect labor costs, businesses can gain a clearer understanding of their labor expenses, make informed financial decisions, and optimize their workforce for improved profitability and competitiveness.
Conclusion
Mastering labor cost calculations is a critical skill for businesses looking to optimize their financial performance, make informed decisions, and remain competitive in their industries. Throughout this guide, we have explored the key concepts and formulas needed to accurately calculate and manage labor costs.
We began by defining labor costs and discussing the importance of understanding these expenses for businesses of all sizes. We then delved into the methods for calculating hourly, annual, and project-based labor costs, providing step-by-step formulas and practical examples.
Furthermore, we examined the concept of labor cost percentage and its significance in assessing financial health, efficiency, and profitability. We also highlighted the differences between direct and indirect labor costs, emphasizing the importance of accurate categorization for cost allocation, pricing, and budgeting.
In addition to the calculation methods, we provided strategies for optimizing labor costs, such as implementing efficient scheduling, investing in employee training, and automating processes where possible. By regularly reviewing and analyzing labor cost data, businesses can identify areas for improvement and make data-driven decisions that support long-term growth and success.
To put these insights into action, we recommend the following steps:
- Review your current labor cost tracking and calculation methods to ensure accuracy and completeness
- Implement the formulas and strategies discussed in this guide to improve your labor cost management
- Regularly monitor and analyze your labor cost data to identify trends, inefficiencies, and opportunities for optimization
- Communicate labor cost insights to key stakeholders and decision-makers to foster a data-driven culture and support informed decision-making
- Continuously refine your labor cost management practices based on industry best practices, technological advancements, and evolving business needs
By mastering labor cost calculations and implementing effective management strategies, businesses can unlock the full potential of their workforce, drive profitability, and achieve long-term success in an increasingly competitive landscape.