Labor costs are a critical component of any business's expenses, representing the total amount of money spent on employee wages, salaries, and benefits. These costs can be divided into two main categories: direct labor costs and indirect labor, with direct labor costs associated with the production of goods or services, such as wages paid to assembly line workers or service technicians. Indirect labor costs include expenses like salaries for supervisors, managers, and support staff, as well as employee benefits and taxes.
Accurate labor cost calculation is essential for the success of any business, as it directly impacts pricing, profitability, and overall financial health. By understanding the true cost of labor, companies can make informed decisions about pricing strategies, resource allocation, and growth opportunities. Some of the key reasons why accurate labor cost calculation matters include:
- Ensuring accurate pricing: By knowing the true cost of labor, businesses can set prices that cover their expenses and generate a profit.
- Maintaining profitability: Accurate labor cost calculations help companies identify areas where they may be overspending or undercharging, allowing them to make necessary adjustments to maintain profitability.
- Facilitating budgeting and forecasting: With a clear understanding of labor costs, businesses can create more accurate budgets and financial forecasts, enabling better decision-making and planning.
- Complying with regulations: Properly calculating labor costs ensures compliance with various labor laws and regulations, such as minimum wage requirements and overtime pay.
Labor costs can vary significantly across industries, potentially accounting for 4.7% to 33% of sales. This variation highlights the importance of industry-specific strategies to manage labor costs effectively. For instance, regular comparisons of sales data with employee scheduling can help identify the most cost-effective staffing levels, potentially reducing unnecessary overtime costs that can quickly erode profit margins.
Failing to accurately calculate labor costs can lead to a range of negative consequences for businesses, including:
- Undercharging for products or services, leading to reduced profits or even financial losses.
- Overcharging, which can result in a loss of customers and market share to competitors.
- Difficulty in creating accurate budgets and forecasts, leading to poor decision-making and resource allocation.
- Potential legal and financial penalties for non-compliance with labor laws and regulations.
Given the critical importance of accurate labor cost calculation, it is essential for businesses to understand the common pitfalls and best practices associated with this process. By taking steps to ensure the accuracy of their labor cost calculations, companies can position themselves for long-term success and growth.
Common Pitfalls in Labor Cost Calculation
Many businesses struggle with accurately calculating their labor costs, often due to a variety of common mistakes and oversights. These pitfalls can lead to a distorted view of a company's true labor expenses, resulting in poor decision-making and financial instability. Some of the most frequent errors in labor cost calculation include:
-
Overlooking indirect labor costs and overhead expenses: Indirect labor costs, such as salaries for supervisors, managers, and support staff, are often overlooked when calculating total labor costs. Additionally, overhead expenses like rent, utilities, and equipment maintenance should be factored into labor cost calculations, as they contribute to the overall cost of doing business.
-
Failing to account for employee benefits and taxes: Employee benefits, such as health insurance, retirement plans, and paid time off, can significantly increase labor costs. Failing to include these expenses in labor cost calculations can lead to a substantial underestimation of total labor expenses. Similarly, neglecting to account for payroll taxes, workers' compensation insurance, and other mandatory employer contributions can skew labor cost calculations.
-
Using outdated or incomplete data for calculations: Relying on outdated or incomplete data when calculating labor costs can result in inaccurate estimates. For example, using old wage rates or failing to account for recent changes in employee benefits can lead to misrepresentations of current labor expenses. It is crucial to use the most current and comprehensive data available when performing labor cost calculations.
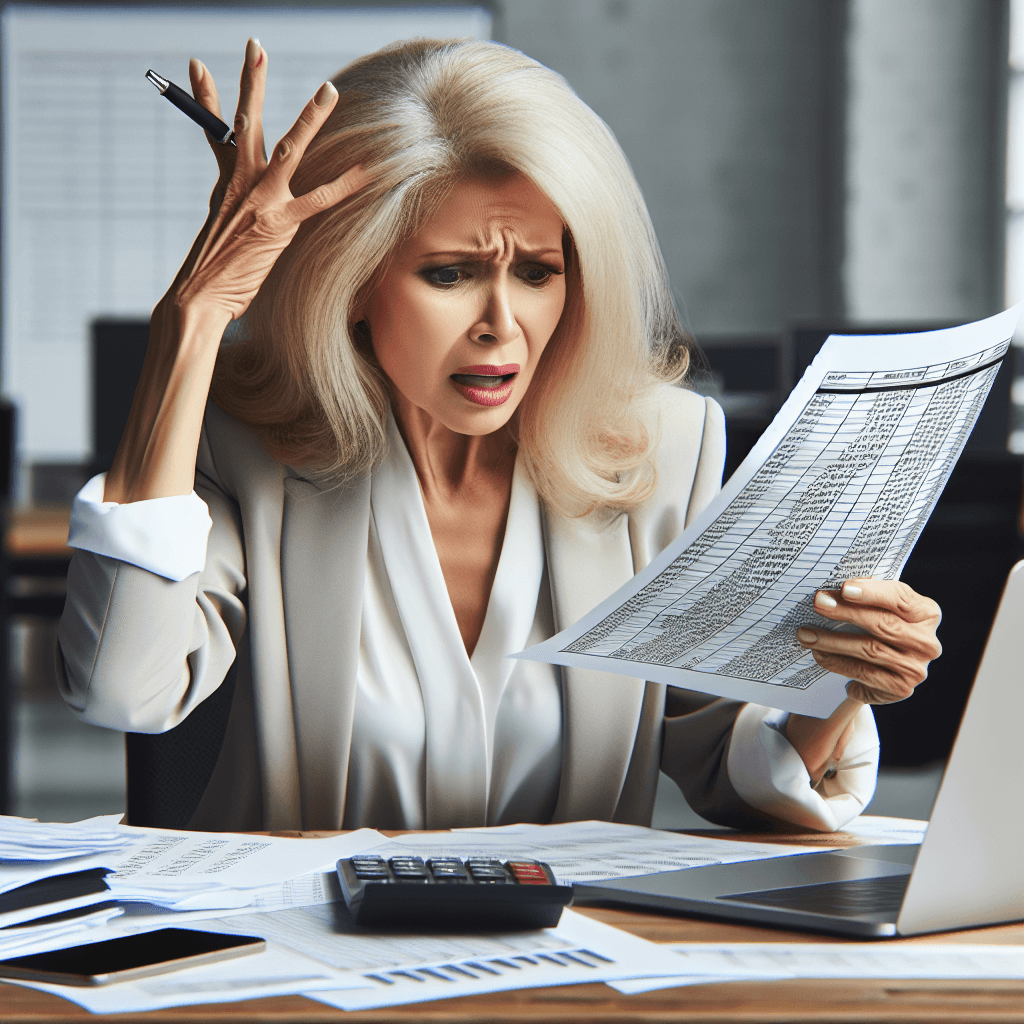
To illustrate the impact of these common pitfalls, consider the following example:
Expense Category | Incorrect Calculation | Correct Calculation |
---|---|---|
Direct Labor | $100,000 | $100,000 |
Indirect Labor | $0 | $50,000 |
Employee Benefits | $0 | $30,000 |
Payroll Taxes | $0 | $15,000 |
Total Labor Costs | $100,000 | $195,000 |
In this example, the incorrect calculation only accounts for direct labor costs, while the correct calculation includes indirect labor, employee benefits, and payroll taxes. The difference between the two calculations is substantial, with the correct calculation nearly doubling the total labor costs. This discrepancy highlights the importance of accurately accounting for all labor-related expenses when calculating total labor costs.
By understanding and avoiding these common pitfalls, businesses can develop a more accurate picture of their true labor expenses, enabling them to make informed decisions about pricing, budgeting, and resource allocation. In the following sections, we will explore the impact of inaccurate labor cost calculations on pricing and profitability, as well as strategies for calculating the true labor burden rate.
The Impact of Inaccurate Labor Costs on Pricing and Profitability
Inaccurate labor cost calculations can have a profound impact on a company's pricing strategies and overall profitability. When businesses underestimate their true labor costs, they often inadvertently underprice their products or services. This can lead to a range of negative consequences, including:
-
Reduced profits: When a company undercharges for its products or services, it may struggle to generate sufficient revenue to cover its expenses and turn a profit. Over time, this can erode the business's financial stability and hinder its growth potential.
-
Difficulty competing in the market: Underpricing can make it challenging for a company to compete effectively in its market. While the business may attract customers with lower prices, it may struggle to maintain quality and service levels, leading to customer dissatisfaction and loss of market share.
-
Unsustainable business practices: Consistently undercharging for products or services can create an unsustainable business model. As the company struggles to cover its costs and generate profits, it may be forced to cut corners, reduce quality, or lay off employees, further eroding its competitiveness and reputation.
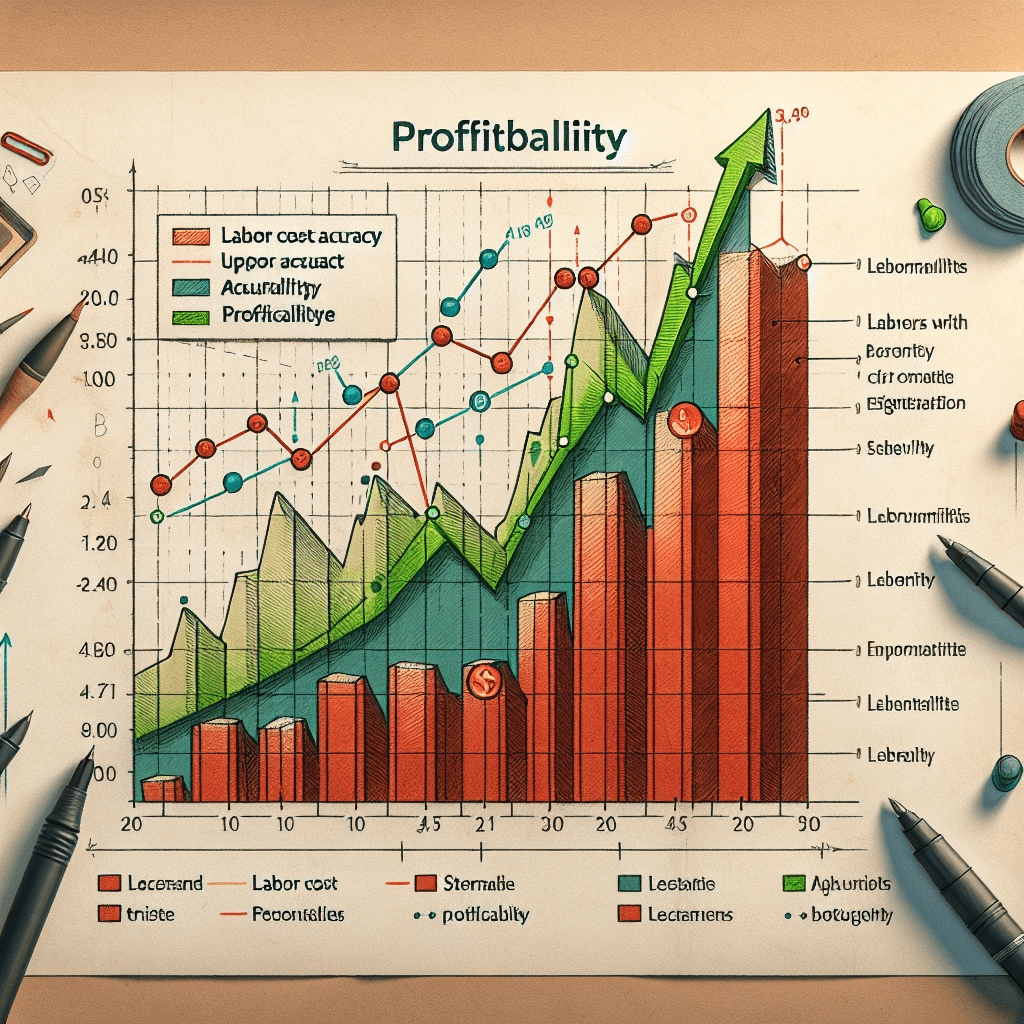
To demonstrate the impact of inaccurate labor costs on pricing and profitability, consider the following scenario:
Item | Accurate Labor Costs | Inaccurate Labor Costs |
---|---|---|
Product Price | $100 | $80 |
Direct Labor | $30 | $30 |
Indirect Labor | $20 | $0 |
Materials | $20 | $20 |
Overhead | $10 | $10 |
Total Costs | $80 | $60 |
Profit per Unit | $20 | $20 |
Units Sold | 1,000 | 1,250 |
Total Profit | $20,000 | $25,000 |
In this example, the company with accurate labor costs charges $100 per unit, while the company with inaccurate labor costs charges only $80 per unit. Although the company with inaccurate labor costs appears to be generating more profit initially due to increased sales volume, it is actually operating on an unsustainable model. By failing to account for indirect labor costs, the company is underpricing its products and may struggle to maintain profitability in the long run.
Over time, the company with inaccurate labor costs may face challenges such as:
- Difficulty covering its true expenses
- Inability to invest in growth or innovation
- Pressure to cut costs in other areas, potentially impacting quality or customer service
- Increased risk of financial instability or bankruptcy
In contrast, the company with accurate labor costs is better positioned for long-term success. By charging prices that accurately reflect its costs, the company can generate sustainable profits, invest in growth and development, and maintain a competitive edge in its market.
Calculating Your True Labor Burden Rate
To accurately assess the full cost of labor, businesses must calculate their labor burden rate. The labor burden rate is the total cost of an employee beyond their hourly wage or salary, including benefits, taxes, and other employer-paid expenses. Understanding and accurately calculating your company's labor burden rate is essential for setting competitive prices, managing costs, and ensuring profitability.
The formula for calculating the labor burden rate is:
Labor Burden Rate = (Total Labor Costs - Base Wages) / Base Wages
To calculate your labor burden rate, follow these steps:
-
Determine your base wages: This is the total amount of hourly wages or salaries paid to employees.
-
Identify all additional labor costs, such as:
- Payroll taxes (e.g., Social Security, Medicare, unemployment insurance)
- Employee benefits (e.g., health insurance, retirement plans, paid time off)
- Workers' compensation insurance
- Other employer-paid expenses (e.g., uniforms, training, equipment)
-
Calculate your total labor costs by adding your base wages and all additional labor costs.
-
Subtract your base wages from your total labor costs to determine your total additional labor costs.
-
Divide your total additional labor costs by your base wages to calculate your labor burden rate.
For example, consider a company with the following labor costs:
Expense Category | Annual Cost |
---|---|
Base Wages | $500,000 |
Payroll Taxes | $50,000 |
Employee Benefits | $75,000 |
Workers' Compensation Insurance | $25,000 |
Other Employer-Paid Expenses | $10,000 |
Using the formula above, we can calculate the labor burden rate:
Total Labor Costs = $500,000 + $50,000 + $75,000 + $25,000 + $10,000 = $660,000
Total Additional Labor Costs = $660,000 - $500,000 = $160,000
Labor Burden Rate = $160,000 / $500,000 = 0.32 or 32%
In this example, the company's labor burden rate is 32%, meaning that for every dollar spent on base wages, the company spends an additional $0.32 on other labor-related expenses.
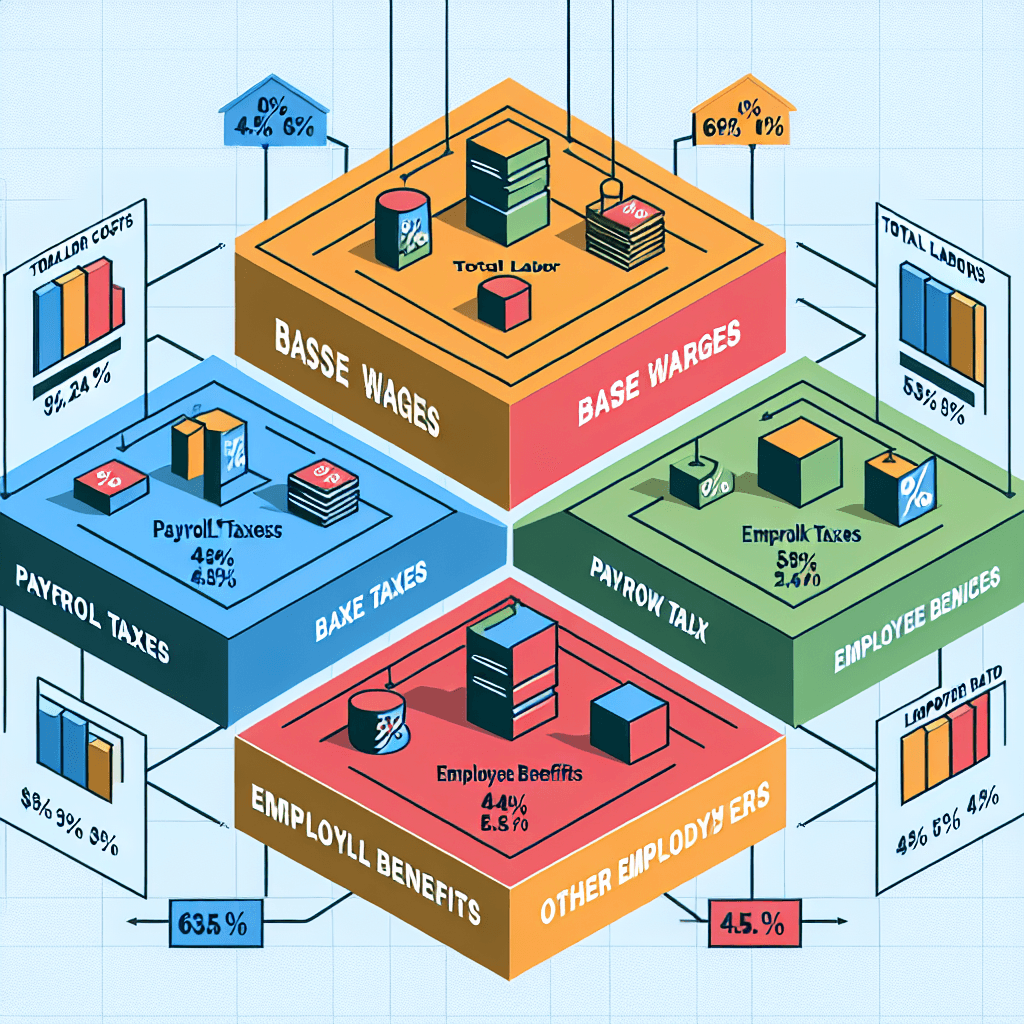
When determining your labor burden rate, it's important to consider factors such as:
- Industry standards and benchmarks
- Regional differences in labor costs and regulations
- Company size and structure
- Specific employee roles and responsibilities
By accurately calculating and understanding your labor burden rate, you can make informed decisions about pricing, budgeting, and resource allocation. This knowledge will help you maintain profitability, remain competitive in your market, and support long-term business growth.
Direct vs. Indirect Labor Costs: What's the Difference?
When calculating labor costs, it's crucial to understand the difference between direct and indirect labor costs. Distinguishing between these two categories helps businesses accurately allocate expenses, set prices, and manage their workforce effectively.
Direct labor costs are expenses directly associated with the production of goods or services. These costs can be easily traced to specific products or projects and typically vary based on the volume of output. Examples of direct labor costs include:
- Wages paid to assembly line workers in a manufacturing plant
- Salaries of service technicians in a repair company
- Hourly pay for construction workers on a building project
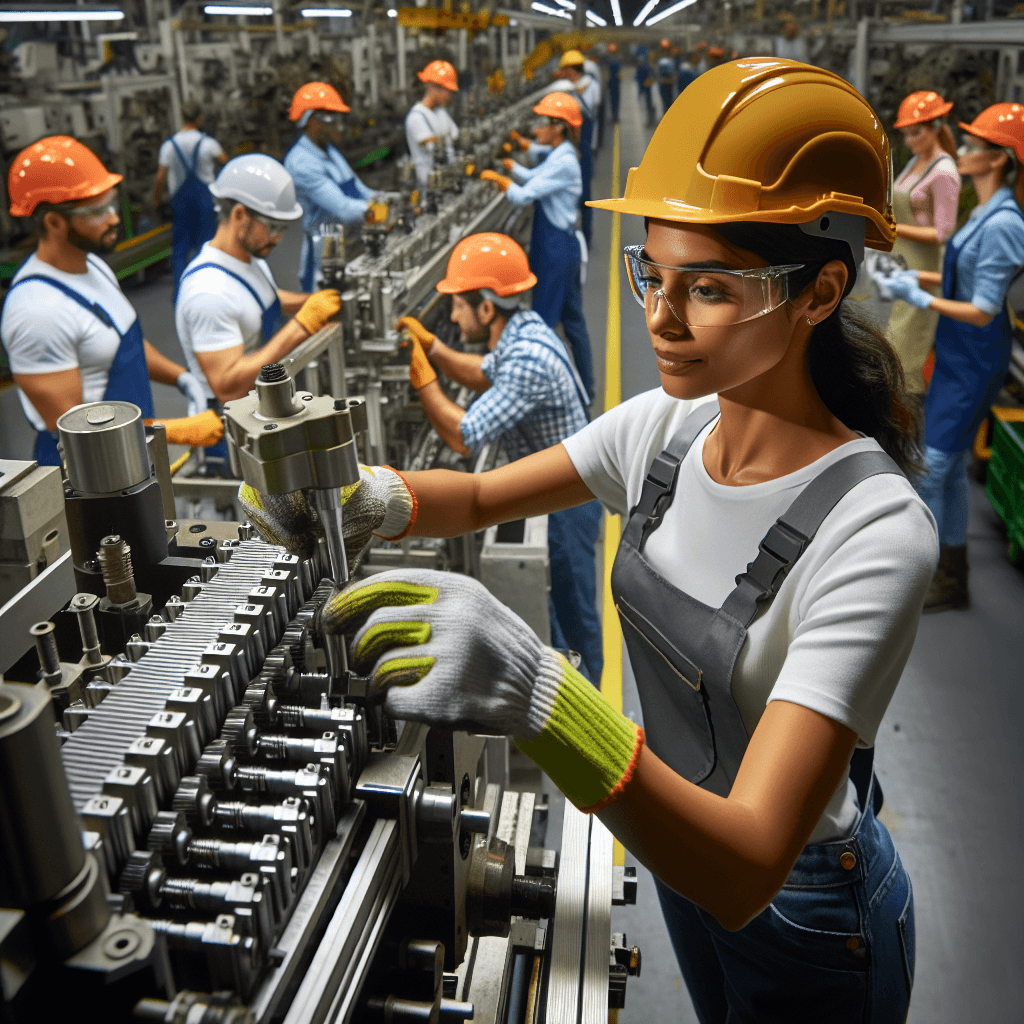
In contrast, indirect labor costs are expenses that support the production process but cannot be directly tied to a specific product or project. These costs are often fixed and do not vary significantly with changes in output. Examples of indirect labor costs include:
- Salaries of supervisors, managers, and administrative staff
- Wages of maintenance and janitorial personnel
- Pay for human resources, accounting, and other support functions
To better understand the difference between direct and indirect labor costs, consider the following example:
Employee Role | Hourly Wage | Hours Worked | Total Cost | Labor Type |
---|---|---|---|---|
Assembly Line Worker | $15 | 160 | $2,400 | Direct |
Service Technician | $20 | 120 | $2,400 | Direct |
Production Manager | $30 | 160 | $4,800 | Indirect |
HR Coordinator | $25 | 160 | $4,000 | Indirect |
In this example, the assembly line worker and service technician are directly involved in producing goods or services and are therefore classified as direct labor. The production manager and HR coordinator, while essential to the company's operations, do not directly contribute to the production process and are classified as indirect labor.
Accurately categorizing labor costs is essential for several reasons:
-
Pricing: Understanding the true cost of direct labor helps businesses set prices that cover their expenses and generate a profit.
-
Budgeting: Separating direct and indirect labor costs allows companies to create more accurate budgets and allocate resources effectively.
-
Cost control: By identifying direct and indirect labor costs, businesses can target areas for cost reduction and process improvement.
-
Decision-making: Knowing the breakdown of direct and indirect labor costs informs decisions about staffing, production, and resource allocation.
By carefully tracking and categorizing direct and indirect labor costs, businesses can gain a clearer picture of their total labor expenses and make data-driven decisions to optimize their workforce and improve overall profitability.
Strategies for Lowering Labor Costs Effectively
While accurate labor cost calculation is essential for maintaining profitability, businesses must also find ways to manage and reduce these expenses without compromising quality or productivity. Implementing effective strategies to lower labor costs can help companies remain competitive, improve their bottom line, and support long-term growth. Some key approaches to reducing labor costs include:
-
Optimizing scheduling and reducing overtime: One of the most effective ways to lower labor costs is to optimize employee scheduling. This involves ensuring that the right number of employees are scheduled for each shift, based on factors such as customer demand, production requirements, and seasonal fluctuations. By carefully managing schedules, businesses can minimize overstaffing and reduce the need for costly overtime hours.
-
Streamlining processes and improving efficiency: Identifying and eliminating inefficiencies in work processes can significantly reduce labor costs. This may involve:
- Analyzing workflows to identify bottlenecks and redundancies
- Implementing lean manufacturing or service delivery principles
- Providing employee training to improve skills and productivity
- Encouraging a culture of continuous improvement and innovation
By streamlining processes and enhancing efficiency, companies can reduce the amount of labor required to produce goods or services, ultimately lowering labor costs.
-
Implementing technology and automation where appropriate: Investing in technology and automation can help businesses reduce labor costs by eliminating the need for certain manual tasks. For example:
- Implementing a customer relationship management (CRM) system to automate sales and customer service processes
- Using robotic process automation (RPA) to handle repetitive administrative tasks
- Adopting machine learning algorithms to optimize inventory management and demand forecasting
While implementing technology and automation may require an initial investment, the long-term labor cost savings can be substantial.
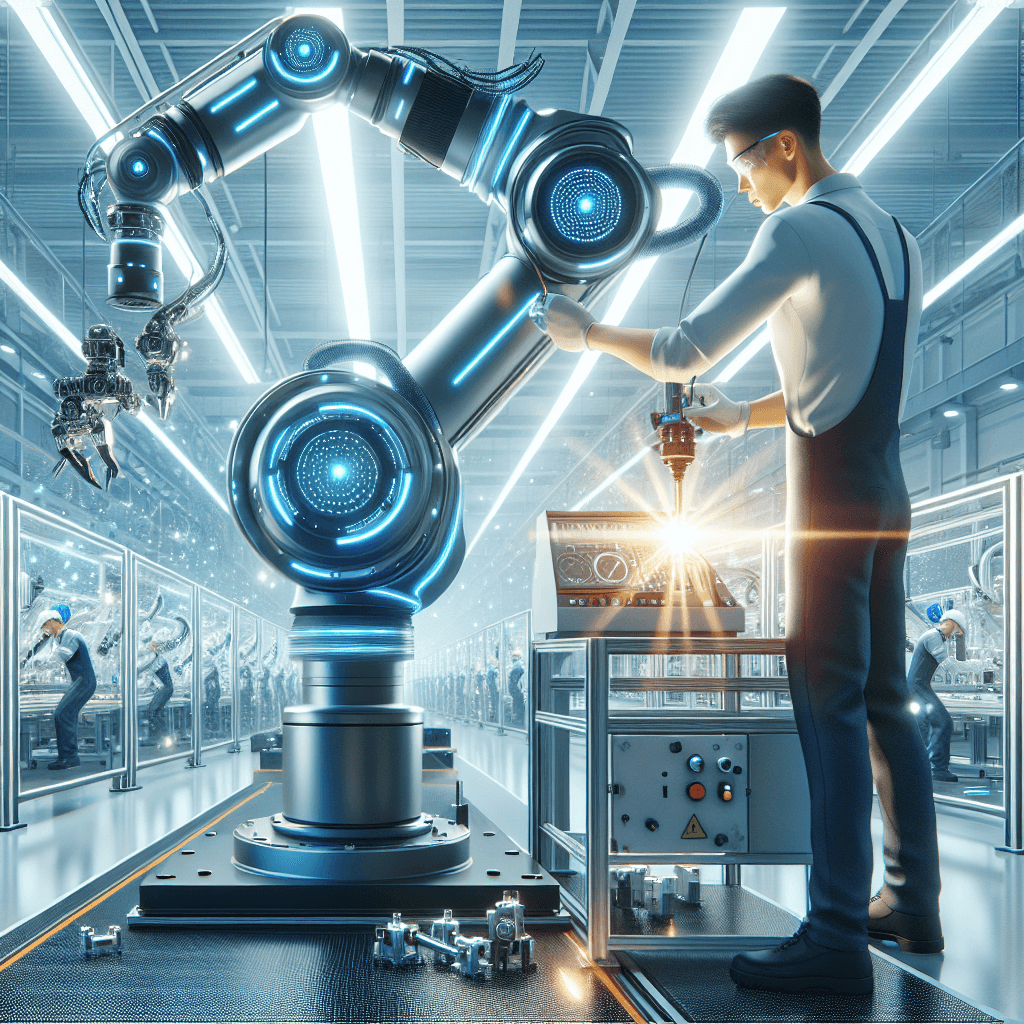
To demonstrate the potential impact of these strategies, consider the following example:
Strategy | Current Labor Hours | Optimized Labor Hours | Hourly Wage | Current Cost | Optimized Cost |
---|---|---|---|---|---|
Scheduling Optimization | 1,000 | 800 | $15 | $15,000 | $12,000 |
Process Improvement | 800 | 700 | $15 | $12,000 | $10,500 |
Automation Implementation | 700 | 500 | $15 | $10,500 | $7,500 |
In this example, the company initially spends $15,000 on labor costs for a specific process. By implementing scheduling optimization, process improvements, and automation, the company can progressively reduce its labor hours and associated costs. The cumulative effect of these strategies results in a 50% reduction in labor costs for this process, from $15,000 to $7,500.
It's important to note that the effectiveness of these strategies will vary depending on factors such as industry, company size, and the nature of the work performed. Additionally, businesses must carefully consider the potential impact of labor cost reduction strategies on employee morale, customer satisfaction, and overall quality. By striking the right balance between cost optimization and maintaining a skilled, engaged workforce, companies can successfully lower labor costs while positioning themselves for long-term success.
The Role of Time Tracking in Accurate Labor Cost Calculation
Accurate time tracking is a critical component of effective labor cost management. By implementing a robust time tracking system, businesses can gain valuable insights into how their employees are spending their time, identify areas for improvement, and make data-driven decisions to optimize labor costs. Some of the key benefits of using a time tracking system include:
-
Improved accuracy: Time tracking systems eliminate the need for manual time entry and reduce the risk of errors associated with paper timesheets or spreadsheets. By automating the time tracking process, businesses can ensure that labor hours are accurately captured and allocated to the appropriate projects or tasks.
-
Real-time visibility: Many time tracking solutions offer real-time dashboards and reporting capabilities, allowing managers to monitor employee productivity, identify bottlenecks, and make timely adjustments to workload distribution or staffing levels.
-
Enhanced compliance: Time tracking systems can help businesses comply with labor laws and regulations, such as the Fair Labor Standards Act (FLSA), by accurately recording employee hours and ensuring that overtime and minimum wage requirements are met.
-
Better cost allocation: By tracking time at the project or task level, businesses can more accurately allocate labor costs to specific initiatives, clients, or departments. This granular data can inform pricing strategies, project budgeting, and resource allocation decisions.
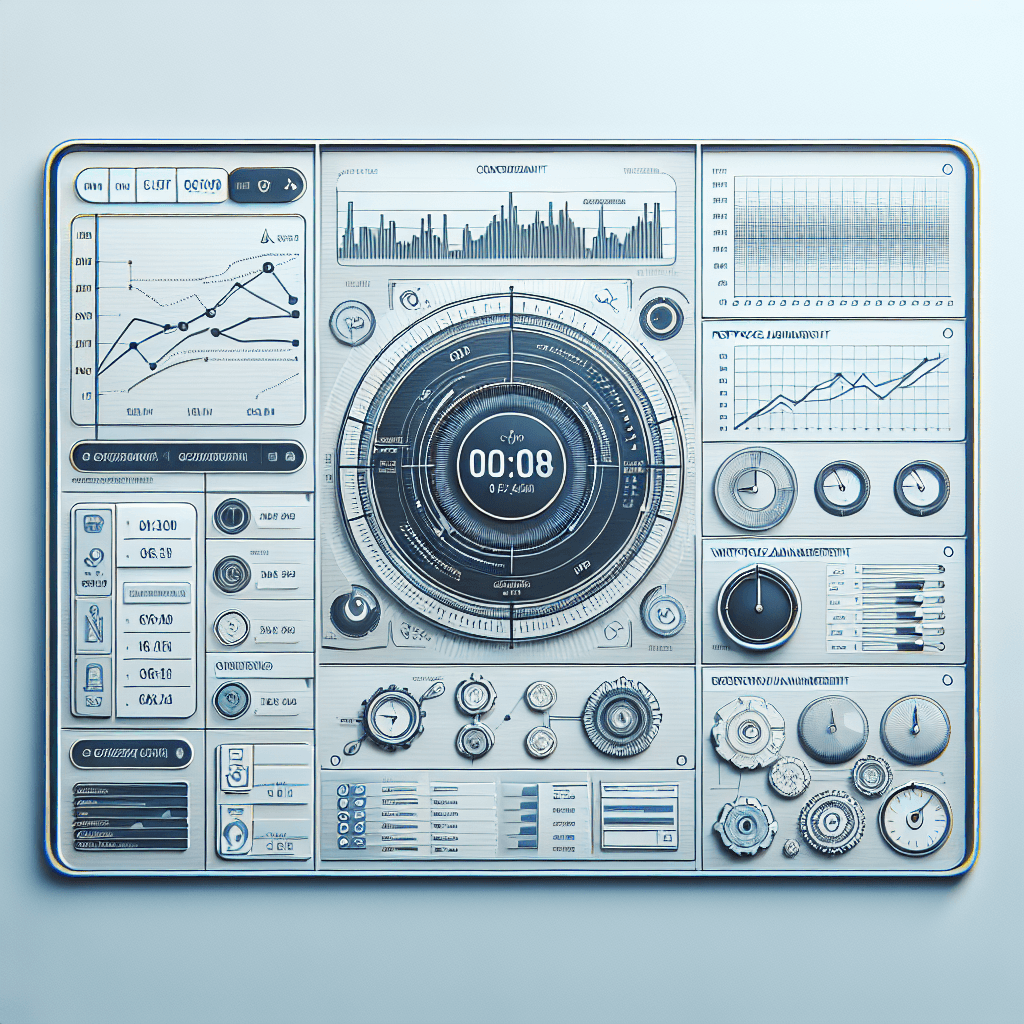
When selecting a time tracking solution, businesses should look for features such as:
- Easy-to-use interfaces for employees to log their time
- Mobile compatibility for remote or field-based workers
- Integration with existing project management or payroll systems
- Customizable reporting and analytics capabilities
- Robust security measures to protect sensitive employee data
To illustrate the impact of time tracking on labor cost calculation, consider the following example:
Employee | Project A (Hours) | Project B (Hours) | Hourly Rate | Total Cost |
---|---|---|---|---|
John | 25 | 15 | $20 | $800 |
Sarah | 20 | 20 | $25 | $1,000 |
Michael | 30 | 10 | $22 | $880 |
Total | 75 | 45 | - | $2,680 |
In this example, the time tracking system allows the business to accurately capture the hours each employee spends on different projects. This data can be used to calculate the total labor costs associated with each project, as well as the overall labor expenses for the company. Armed with this information, the business can make informed decisions about project pricing, resource allocation, and workforce optimization.
By leveraging the power of time tracking, businesses can gain a deeper understanding of their labor costs and make strategic decisions to improve profitability and efficiency. However, it's important to remember that time tracking is just one piece of the labor cost management puzzle. To maximize the benefits of time tracking, businesses must also have clear processes in place for analyzing and acting upon the data collected, as well as a culture that values accuracy, accountability, and continuous improvement.
Conclusion: Mastering Labor Cost Calculation for Business Success
Accurate labor cost calculation is a critical component of effective business management. By understanding the true cost of labor, businesses can make informed decisions about pricing, budgeting, and resource allocation, ultimately driving profitability and long-term success.
Throughout this article, we've explored the key concepts and strategies related to labor cost calculation, including:
- Understanding the components of labor costs and the importance of accurate calculation
- Identifying common pitfalls in labor cost calculation and how to avoid them
- Assessing the impact of inaccurate labor costs on pricing and profitability
- Calculating the true labor burden rate and its significance in decision-making
- Distinguishing between direct and indirect labor costs and their roles in cost allocation
- Implementing strategies for effectively lowering labor costs without compromising quality
- Leveraging time tracking systems to improve accuracy, visibility, and compliance in labor cost management
By mastering these concepts and implementing the strategies discussed, businesses can take control of their labor costs and position themselves for success in an increasingly competitive marketplace.
However, the journey to effective labor cost management is an ongoing process. As businesses grow and evolve, it's essential to regularly review and update labor cost calculations, assess the effectiveness of cost optimization strategies, and continuously seek opportunities for improvement.
To get started on the path to more accurate and effective labor cost management, consider the following action steps:
- Conduct a thorough review of your current labor cost calculation processes, identifying any gaps or areas for improvement.
- Implement a robust time tracking system to capture accurate labor data and gain real-time visibility into employee productivity and project costs.
- Analyze your labor cost data regularly, using insights to inform pricing strategies, project budgeting, and resource allocation decisions.
- Foster a culture of continuous improvement, encouraging employees to identify and suggest opportunities for process optimization and cost reduction.
- Stay informed about industry trends, best practices, and emerging technologies related to labor cost management, and be prepared to adapt your strategies as needed.
By taking a proactive and data-driven approach to labor cost calculation and management, businesses can unlock the full potential of their workforce, drive profitability, and secure a competitive edge in their markets. The path to success starts with a commitment to accuracy, transparency, and continuous improvement in all aspects of labor cost management.